증류탑내에 trap된 minor한 성분들이 반응하여 solid를 생성할 수 있고 이는 major problem의 원인이 되기도 한다. 이에 따른 conventional 대응 방법으로는 주로 이미 생성된 solid에 focus를 맞추지만 운전조건을 변경함에 의해 solid 생성을 방지하거나 최소화하는 전략이 필요하다.
증류과정에서 열에 민감한 minor한 물질들은 고온에 노출시 반응을 하여 solid나 polymer를 생성하거나 heavy한 성분이 되어 증류탑의 특정 영역에서는 액체내에 완벽한 soluble상태로 있지 않을 수 있다.
이로 인해 예측하지 못한 vapor-liquid contact을 야기하여 product quality에 영향을 주고 plant downtime이 커지고 maintenance 비용도 증가하게 된다.
이러한 상황에서 쉽게 접근할 수 있는 방법이 생성된 solid를 잘 처리하도록 internals이나 tray를 변경하거나, 반응성 물질들의 반응을 억제하거나 solid를 분산시키도록 additive를 주입할 수도 있다.
하지만 이러한 방법들은 많은 비용이 요구되며 보다 근본적인 대응방법이 아니다. 따라서 column운전을 주의 깊게 살펴보고, minor component들을 공정으로부터 퍼지하는 방법이 더 좋은 결과로 이어질 수 있다.
아래의 예는 ADN (adiponitrile) 생산의 마지막 단계로서, crude ADN stream으로부터 low boiling point들인 SN (succinonitrile)과 AN (acrylonitrile)을 제거하기 위한 stripper column이다.
이 column 상부의 distillate stream에는 저비점 성분들이 제거되고, bottoms stream에는 주로 ADN이며 저비점 불순물의 trace와 고비점 성분이 포함되어 추가 정제를 위해 후단으로 이송한다. 열에 민감한 물질을 증류함에 따라 column은 진공으로 운전을 하며, feed 위, 아래에는 structured packing bed가 설치되어 있다.
아래 figure1에 따르면 distillate flow rate의 set point는 운전원이 설정하고, reflux유량은 accumulator level에 의해 cascade운전을 한다. reboiler heat source인 steam유량의 set point는 운전원이 설정하고 bottoms 유량 역시 column bottom level에 의해 cascade제어되고 있다. column overhead압력은 vacuum ejector spillback을 통해 제어되며 이 공정에는 온도제어가 없다.
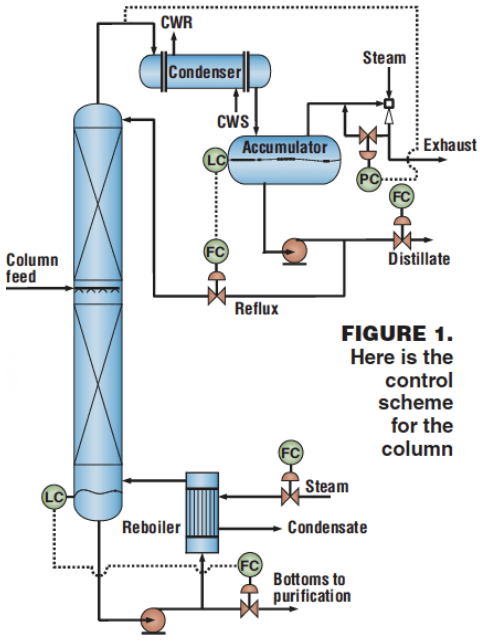
이 column은 feed point 상부 packing에서 polymer 생성으로 인해 심각한 fouling에 의해 runtime이 제약을 받는 운전상 문제가 있었다.
운전 초기 유체가 clean할 경우 distillate stream내 최소한의 product loss와 함께 on spec을 유지할 수 있었다. 하지만 이후 압력이 천천히 build-up되고 결국 process upset이 몇시간 지속이 되었다.
이 때 column압력 증가로 인해 자체적으로 압력을 배출하게 되면 운전조건은 다시 정상으로 복귀하여 column은 다시 압력이 build-up되기 까지 운전을 하였다. 하지만 이러한 반복적인 비정상 운전이 6개월 정도 지속된 후 운전은 더욱 심각해져서 flooding을 야기하여 distillate stream으로 product loss가 증가하게 되었다. 결국 column은 on spec을 맞출 수 없었고 1년마다 청소 및 packing 교체를 위해 shut down을 하여 생산 손실 및 유지관리 비용이 증가하게 되었다.
shut down후 검사를 해보면 structured packing이 완전히 fouling으로 plugged되었고 이는 polymer의 점진적인 build-up 및 packing의 plugging으로 인해 column의 분리효율이 크게 저하된 결과였다.
Initial troubleshooting
문제를 해결하기 위해 전문가팀은 초기에 solid를 제거하여 fouling으로 인한 비용을 줄이기 위해 column internals을 변경하는 제안을 하였고, 아울러 다양한 structured packing의 배치를 고려하고 product spec을 맞추기 위한 분리를 하면서 fouling이 시작될 때 solid를 제거할 수 있도록 설계에 반영하였다.
하지만 이 과정에서 tall bed에 liquid redistributor가 없음을 알았고 이로 인해 channeling에 따른 liquid maldistribution을 야기하여 liquid stagnant pocket이 생겼고 결국 fouling으로 이어졌다.
분석결과 fouling은 부적절하고 비효율적인 기액 접촉의 결과이었으며, column internal 변경에 대한 합리적 근거로 기액접촉의 개선을 통해 분리효율을 높이고 전체적인 column 운전을 개선하고 fouling을 줄일 수 있었다.
대안 분석
하지만 이미 이전의 trouble로 인해 column internals이 변경되었으며 이번에 또 다시 변경을 할 경우의 예상이 부정적이었고 최적의 해결책은 비현실적이었다. 더우기 liquid maldistribution이나 vapor bypassing이 실질적인 문제이었다면 column 운전을 통한 원하는 분리를 제대로 할 수 없었다. 그래서 기액접촉 효율 개선과 fouling문제를 최소화하기 위해 column internal을 변경하는 것이 불확실하고 성공에 대한 확률이 낮았다.
반면, maintenance shutdown때 structured packing에 대한 검사를 통해 fouling product들이 다른 공정에서 사용되었던 nitrile process chemistries의 특징이었음을 알 수 있었다.
foulant의 화학적 분석 결과, top side의 fouling은 cyanide type polymerization에 따라 발생되었음을 확인했고 이러한 type의 polymerization은 커피 찌꺼기와 유사한 solid를 만들어 고온에 노출시 검은 tar모양의 물질로 변하는 경향이 있었다. 아울러 이러한 polymerization은 autocatalytic하여 일단 polymerization이 시작하면 반응속도는 더욱 빨라지고 고온에 의해 더욱 더 빨라지게 된다.
비록 column이 진공으로 운전이 되지만 내부의 운전조건은 화학적 반응에 적절한 조건이 되어 cyanide type polymer의 확인을 통해 polymer를 만드는 반응에 참여하는 compound의 존재를 인지하였고 이 조성이 SN (succinonitrile)이었음을 예상할 수 있었다.
SN의 존재로 인해 예상되었던 trouble은 product loss를 줄이기 위해 distillate flow rate를 control하기 위한 근거와 일치했다.
SN과 ADN은 boiling point가 유사하여, ADN으로부터 SN을 분리하거나 column내 SN trapping없이 distillate stream내에서 ADN을 최소화는 두 가지 목적을 달성하기가 쉽지 않다.
column 내부에서는 SN이 AN과 HCN (hydrogen cyanide)으로 열분해되고 이중 HCN이 light하여 overhead product를 따라 퍼지된다. 그러나 HCN의 반응성 측면에서 일단 생성이 되면 polymerization반응을 멈출 수 없다는 것을 알았다. SN농도를 낮출 수 있는 방법이 process upset이며, SN농도가 증가하여 SN분해반응의 생성물 중 light 성분이 column에서 빠져 나가지 못해 운전이 불안정해지고 압력이 증가하며 결국 process upset을 야기했다.
일단 column이 퍼지된 후 압력이 정상상태로 복귀하면 SN의 누적이 다시 시작되고, 시간이 갈수록 악화되며 결국 polymer성장으로 인해 vapor, liquid의 path를 완벽히 방해하며 column을 정상적으로 운전을 할 수 없고 결국 off spec을 야기하게 된다.
만약 column운전조건을 변경하여 많은 SN을 퍼지하도록 path를 제공하면 fouling의 source가 감소된다.
simulation 스터디 결과 overhead distillate유량을 단순히 증가함에 의해 column내 SN농도를 크게 줄여 fouling속도를 낮추고 column run time을 늘릴 수 있었다.
steady state simulation
조성이 column내에서 trap되고 accumulation되는 것은 unsteady proces이므로 steady state simulation이 무의미할 수 있지만, trap성분의 가능성과 관련하여 공정 시스템의 본질적 특징이나 경향성을 인지하는 screening tool로 활용될 수 있다.
위 figure 1에 대해 simulation을 수행하여 reboiler heat duty와 distillate flow rate를 specify하고, plant 운전 data와 column temperature profile이 simulation 결과와 match되도록 column tray efficiency를 adjusting하였다.
figure2는 column내 SN과 ADN의 기상 조성 profile을 보여준다. simulation결과는 실제 운전 data와 잘 match가 되었고, distillate stream내 ADN이 매우 소량 존재하며, distillate와 bottoms를 통해 소량의 SN이 퍼지되었다.

관찰된 key componet는 정상운전중 column내 trap된 SN의 높은 농도이며 fouling의 source가 된다. figure2에서 SN bubble의 peak 위치가 실제 column의 중간 지점보다 약간 위이며 column 운전상 fouling이 가장 심한 section과 거의 일치한다.
simulation결과 distillate유량이 증가하면 SN은 더 완벽히 퍼지가 된다. 아울러 column내 SN의 기상 조성 profile을 보면 distillate유량이 증가함에 따라 column내 bubble이 위쪽으로 이동했음을 알 수 있다. (Figures 3 and 4)
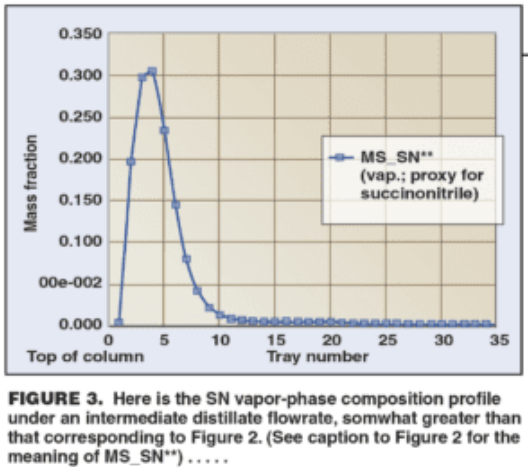
그리고 peak SN농도도 70%에서 intermediate distillate 유량에서 30%로 줄었고 (figure3), high distillate 유량에서는 15%로 더 줄었다. (figure4)

이 steady state process simulation 스터디를 통해 column clean-up이후 start-up시 곧바로 distillate유량을 늘려 column을 운전하도록 recommend하였다. 이는 별도로 비용이 발생되는 것이 아니므로 즉시 수행을 하여 짧은 시간내에 그 효과성이 입증이 되었고 column은 압력 증가나 relief상황이 일어나지 않았다.
trap component는 주기적으로 반복되는 경향이 있으며 그 빈도는 유입유량, reflux유량, boilup 유량, 온도, 압력 등에 의존한다. 실제로 trap되는 조성의 type이나 본질을 이해하는 것이 중요하며, 때때로 인지하지 못하거나 의도하지 않았던 반응이 문제를 유발하며 분석하기도 어렵다.
한 예로서 반응시스템에는 process stream이 antifoam, inhibitor, dispersant와 같이 성능 개선을 위해 주입된 additive와의 상호 작용으로 원치 않은 성분을 포함할 수 있다. 그리고 촉매 성능의 변경, 반응 선택도로 인해 minor 성분의 농도 변화가 합성 반응을 개시할 수도 있다.
공정의 화학반응에 대한 이해와 분석계기들에 대한 access를 통해 문제에 대한 본질적인 인지를 할 수 있고, 그 영향을 줄이거나 완전히 제거할 수 있는 방법을 제공할 수 있다.
References
1. Kister, H.Z., Component Trapping in Distillation Towers: Causes, Symptoms, and Cures, Chem. Eng. Prog., Vol. 100, No. 8, pp. 22-33, August 2004.
#additive#purge#ADN#SN#AN#HCN#structured_packing#cascade#fouling#build_up#redistributor#channeling#maldistribution#nitrile#polymerization#autocatalytic#peak#antifoam#boilup
'화학공장 troubleshooting' 카테고리의 다른 글
증류탑 bottleneck troubleshooting (0) | 2025.01.04 |
---|---|
troubleshooting 사례 (0) | 2024.12.28 |
pump troubleshooting (0) | 2024.12.28 |
Deaerator flooding (0) | 2024.12.28 |
열교환기 troubleshooting (0) | 2024.12.28 |