
Batch 반응기는 inlet / outlet 흐름이 없이 미리 채워진 반응물들이 closed vessel 내부에서 주어진 시간동안 반응이 진행되며 이를 위해 mixing을 위한 agitator, 가열 혹은 냉각 장치가 필요할 수 있다.
Batch 반응기는 보통 규모가 작은 공정이나 신규 공정 개발시 testing용 혹은 값비싼 제품을 제조하거나 연속공정으로 전환하기 어려운 경우에 많이 적용된다.
장점은 반응기내 반응물들이 일정한 조성으로 유지하여 전환율이 매우 높지만 단점으로는 수동운전에 따른 운전비가 커지고 제품의 가변성이 있고, batch반응마다 비우고 청소하고 채우는 dead time이 크며 safety issue가 있다.
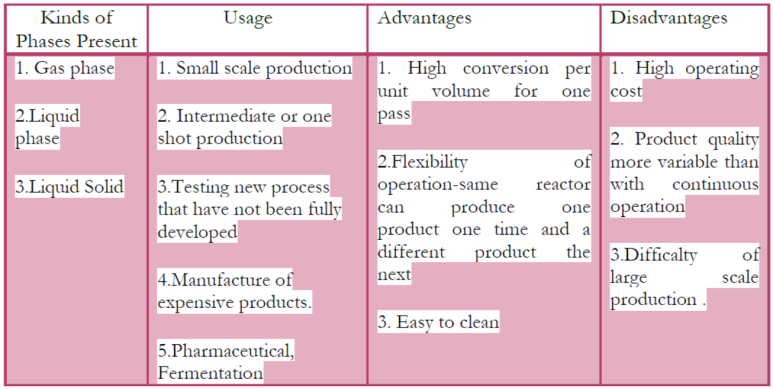

Semi batch 반응기
회분식 반응을 통해 증발된 vapor를 응축, refluxing하여 반응열에 따른 heat accumulation을 제거하며 heat balance 최적화를 위해 condenser는 2 stage 열교환기를 적용하여 첫번째는 chilled water로, 두번째는 더 낮은 온도의 brine을 이용할 수 있다. Vacuum reaction인 경우 overhead condenser와 collection receiver사이에 equalization line을 고려한다.
Batch reactor에서 distillation rate 계산
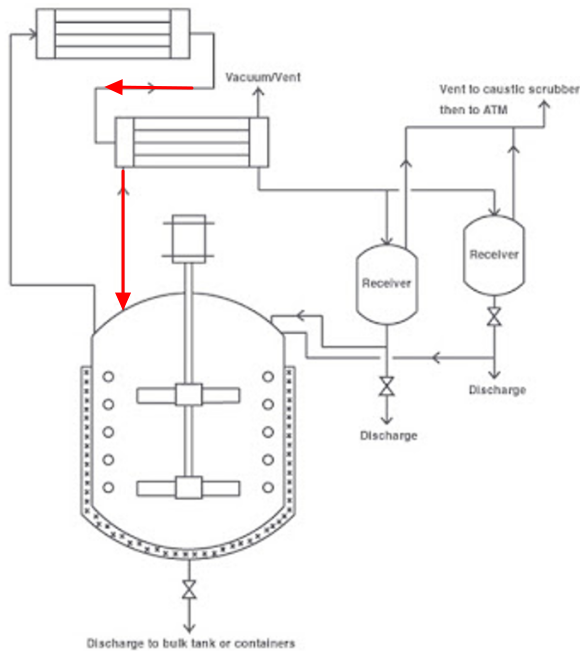
반응 이후, 불순물 제거를 위해 solvent를 이용하여 product를 농축하는데, Raw material로부터 물을 제거하는 것으로서 raw material은 solvent에 녹여 이후 진공 상태에서 solvent는 distillation되고, 이 때 물분자도 제거가 되는데 이는 물에 민감한 product를 다룰 때 적용한다.
예를 들어 Ethyl acetate가 있는 반응기는 650mmHg의 진공과 30도에서 반응이 진행되며 10m3의 capacity이고 재질은 SS316이며 액체 부피는 5m3이다. 10m3일 경우 19.82m2의 전열면적을 갖지만 (H/D=1.5 가정) liquid level까지의 effective area는 19.82 x 0.5 = 9.91 m2이다.
밀도는 897 kg/m3이고, 비열은 0.454 KCal/Kg.K, 증발잠열은 87.6 KCal/Kg임. SS316에 대해 U값은 250 Kcal/m2hK로 가정한다. spec상 batch 내용물이 40도를 초과해서는 안됨에 따라 utility로서 steam 대신 hot water를 사용하고 Delta T는 10도를 고려하여 hot water온도는 50도를 사용한다. 반응기 온도가 25도이고 HW는 50도가 45도로 냉각된다.
LMTD = ( ( 50 - 25 ) - ( 45 - 25 ) ) / Ln [ ( 50 -25 ) / ( 45 - 25 ) ]
= 5 / Ln [ 1.25 ] = 22.727 Deg C,
반응기 jacket을 통해 전달된 열량, Q = U x A x LMTD = 250 x 9.91 x 22.727 = 56,306.143 Kcal
반면, 반응기 내부의 heat duty계산
Qhl = Sensible heat + Latent heat
= M x Cp x dT + M1 x λ (M은 반응기 내부 전체양이며 M1은 증발되는 양임)
= (V x ρ) x Cp x dT + M1 x λ
= 5 x 897 x 0.454 x (30-25) + M1 x 87.6
= 10,180.95 + M1 x 87.6
10,180.95 + M1 x 87.6 = 56,306.143
M1 x 87.6 = 46,125.192
M1 = 526.54 Kgs of Ethyl Acetate = (526.54 / 0.897) Liter of ethyl acetate
M1 = 587 Liter of Ethyl Acetate vaporized
U값은 사용되는 utility에 의존하지만 일반적으로 100-150 Kcal/hr.Sq.m.K을 적용함. U값은 개별 film coefficient와 열전도도, 두께로 계산되며, 개별 coefficient는 열전도도와 Re. No., Pr. No에 의존한다. Pr. No.는 다시 열전도도에 의존하므로 OHTC는 주로 metal의 열전도도에 의존함에 따라, SS316 열전도도는 13~17 w/mk, MSGL (Mild Steel Glass Lined)은 5~8w/mk, hastelloy는 30~35w/mk의 범위이다. 이를 기준으로 보면, SS316 OHTC는 250-300 Kcal/m2.hr.C, MSGL는 100-150 Kcal/m2.hr.C, hastelloy는 300 KCal/m2.hr.C 이상이다.
다른 예로서 boil-up 증발량을 산출하기 위해, 5m3반응기에 대해 전열면적은 약 12.7m2이며, 3m3 액체 부피에 대한 전열면적은 7.2m2임. SS316에 대한 U값은 약 250 KCal/hr.m2.C이며 스팀은 120도로 가정하면 LMTD는 120-100=20도가 된다. 잠열이 540kcal/kg이므로 boil-up 증발량은 250 X 7.2 X 20/540 = 66.67 kg임.
batch 반응기에서 분리에 필요한 시간

반응기 shell 두께, 내경, 길이에 대한 정보 그리고 반응기 내부 물질양과 분리할 양에 대한 정보, 밀도, 비열, 조성, 열전도도 등 물성치에 대한 정보가 필요하다.
열전달 표면은 SS316을 적용하고 jacket coil은 SS304를 고려하며 가끔 pH에 민감한 분리에는 GLR을 이용한다.
Material Thermal Conductivity, K [W/m.K]
SS304 10-13
SS316 13-17
GLR 1.2-1.5
반응기내 전체 물질에 대해 온도를 올리는 현열은,
Sh = M/t * Cp * dT,
M - mass flowrate = Volume * Density (반응기 내 전체 양)
Cp - Specific heat @ distillation temp
dT - Distillation temp. - RT temp.
잠열 계산
Lh = M * λ
M - Mass flowrate = volume of distillate * Density (증발되는 양)
λ - latent heat of vapor solvent
전열면적을 통해 시간당 이동되는 열량 계산
Q= K * A * dT * (1/X)
K - thermal Conductivity
A - Heat Transfer Area,
dT - Temp. Difference= Distillation temp. -RT temp.
X – thickness (10mm로 가정)
Overall heat load를 시간당 이동된 열량으로 나누어 시간을 구한다.
t= ((M * Cp * dT) + (M * λ))/(K * A * dT), Sec
예) GLR Batch 반응기 capacity는 5m3이고 여기에서 메탄올 1m3을 분리해야 한다. 80% level을 간주하여 4m3이 액체 부피일 때 분리를 위해 필요한 시간을 계산하라. (RT는 25도 고려)
5m3에 대한 전열면적은 12.4m2이며 available heat transfer area는 80%를 고려한 9.9m2임. MSGL의 열전도는 1.2 w/m.k = 0.029 KCal/m.Sec.K로 가정함. 메탄올 비열은 0.45 KCal/Kg.K, 잠열은 264 KCal/Kg, 밀도는 790kg/m3, boiling temp는 64도임.
Sensible heat load = M x Cp x dT = 4 x 790 x 0.45 x (64 - 25) = 56,880 KCal,
Latent heat load = M x λ = 1 x 790 x 264 = 208,560 KCal.
Total Heat load = 265,440 Kcal
전열면적을 통해 이동한 열량 = K x A x dT = 0.029 x 9.9 x (64-25) = 11.52 kcal
즉, 1m3 메탄올을 분리하기 위한 시간은 265,440 / 11.52 = 23,279 Sec = 388 mins = 6.47 hrs 임.
Heating/cooling에 필요한 시간
재질의 물리적, 열적 물성치에 근거한 계산 및 utility에 근거한 계산이 있으며 먼저 heat load를 계산한다.
Q= M/t x Cp x dT
M - Mass flowrate - Volumetric Flowrate x Density,
Cp - Specific Heat Capacity,
dT - Temperature difference of the Mixture
(t2-t1) for Heating, (t1-t2 ) for Cooling.
U값에 근거한 heat load는 다음과 같다.
Q= U x A x (dT)ln
U - Overall Heat Transfer Co-efficient,
A - Heat Transfer Area,
(dT)ln - Log Mean Temperature Difference - ((T - t1) - (T - t2))/Log[( T - t1 )/( T- t2 )],
M/t x Cp x dT = U x A x ( dT )ln = U x A x (( T - t1)-( T - t2 ))/Log[( T - t1 )/( T- t2 )],
Heating/Cooling에 필요한 시간 = [ M x Cp x Log(( T - t1 )/( T- t2 )) ] / ( U x A ).
위 계산은 이론적인 배경이며 heating시간을 계산하기 위해 fourier 열전도도 식을 이용하고, 시간이 지남에 따라 fouling, scaling등으로 열전달 효율이 줄어들게 됨. 아울러 wearing이나 tearing도 영향을 준다. 일반적으로 반응기 jacket은 매 3년마다 descaling을 한다. 이를 위해 15% NaOCl solution을 이용하며 만약 scaling정도가 심하다면 sulfamic acid를 이용할 수 있다.
반응기 전열면적 계산
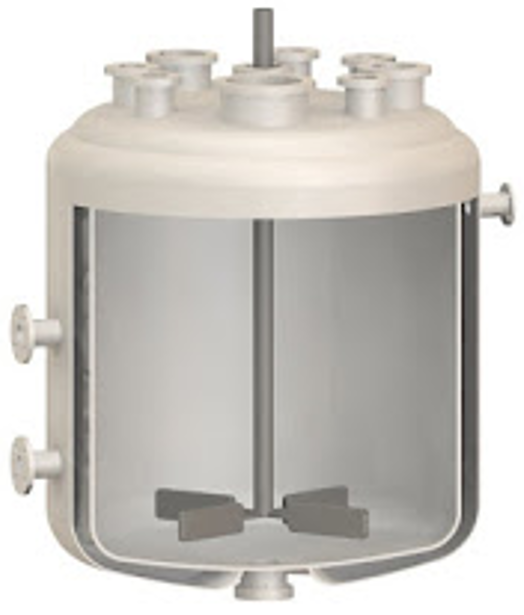
반응, 추출, 분리, pH처리 등을 수행하는 반응기들은 다양한 재질을 사용하며 그 중 SSR (SS reactor), GLR (Glass Lined Reactor), MSGLR (Mild Steel Glass Lined Reactors), PPR (Poly Propylene Reactors)를 사용한다. SSR은 SS316, SS304를 사용함.
SS304에는 Cr이 18~20%, Ni이 8~10%이고, SS316에는 Cr이 16~18%, Ni이 10~14%로 차이가 나지만 가장 중요한 것은 Mo으로서 SS304에는 전혀 없지만, SS316에는 2~3%가 있다. 바닷물 속의 chloride에 대한 부식 저항성을 키우기 위해 몰리브덴을 추가한 SS316을 사용하므로 바닷가 주변 공장은 304 대신 316을 사용한다.
L/D ratio는 1.2~1.6을 적용하며 보통 1.3을 고려함. Volume은 0.2m3에 대해...
Volume of Reactor(0.2)=(Cylindrical Volume + Torispherical Dish volume)
=((Pi*r*r*l)+((Pi/24)*D*D*D))
=((Pi*(D/2)*(D/2)*(1.3D))+((Pi/24)*D*D*D)))
=(1.022+0.1311)*D*D*D
0.2 =1.153*D*D*D
D=0.5576 m=0.56 m, L=0.728 m=0.73 m,
전열면적은 높이 * 원둘레가 되어, = (2*Pi*r) * (L)
= (2*3.147*(0.56/2)) * (0.73)
= 1.2864 Sq.m= 1.29 Sq.m
Area of a torispherical dish = (𝝅 / 4) x ((1.147 x D)^2) = (3.141/4) x ((1.147 x 0.5576)^2)
= 0.785 x 0.409 = 0.32 Sq.m
Total heat transfer area of the reactor = Area of cylinder + Area of torispherical dish
= 1.29 + 0.32 = 1.61 Sq.m

#회분식#batch#jacket#baffle#agitator#CSTR#OHTC#U#conductivity#전열면적#GLR#몰리브덴
'공정설계' 카테고리의 다른 글
FCC (Fluidized Catalytic Cracking) 기술 비교 (0) | 2025.05.06 |
---|---|
Polyol 이해 (0) | 2025.04.29 |
아민 제조 공정 이해 (0) | 2025.03.30 |
cryogenic service blowdown (Depressurizing) (0) | 2025.03.30 |
ABS/SAN process 이해 (0) | 2025.03.22 |