Trouble shooting은 직관적 감각 및 경험에 의존하여 결정할 부분이 아니며, 과거 경험이나 자료들은 하나의 reference로서, 근본적 원인을 추정하는데 도움을 줄 수는 있으나 그대로 적용해서는 실패할 확률이 높다.
근본적 원인을 찾지 못하고 눈에 보이는 문제만을 해결할 경우 나중에 비슷한 문제가 재발되거나 더 큰 문제가 될 수 있어서 논리적 접근 및 공정에 대한 이해를 바탕으로 근본적인 원인을 찾아 해결책을 강구해야 한다. 따라서 선제적 문제 해결을 통해 열교환기 성능 저하 및 공정 performance 저하를 피하고 설비 손상 및 downtime을 최소화할 수 있다.
하지만 근본적 원인을 찾는 것이 쉽지 않은 이유가 관련된 문제점들이 마치 chain reaction처럼 서로 연관이 되어 있어서 root cause에서 파생된 문제들이 또 다른 문제를 야기하여 복합적인 양상으로 진행됨에 따라 열전달 외에 열역학, 유체역학 분야의 전문가적 지식과 다양한 경험을 통해 troubleshooting간의 시행오차를 줄일 수 있다.
이를 위해 다양한 사례에 대해 인과관계에 대한 학습과 체화 그리고 명확한 판단을 하기 위한 훈련을 통해 실제로 문제에 접했을 때 실패 없이 해결할 수 있는 방안이 좀 더 정확하고 빨리 도출될 수 있을 것이다.
운전중 열교환기 성능에 문제가 되어 process malfunction이나 제품의 off spec이 야기될 경우 열교환기 design spec과 제작도면, 현재의 운전조건 (유량, 온도, 압력)을 설계치와 비교, 정비 이력을 수집 및 파악하여 이에 맞는 적절한 조치를 해야 한다. 이를 위해 자료 및 검사를 통한 운전상 문제점을 인지하고, 운전상 문제의 원인을 분석하고, resolution을 제시하여 수행하는 절차로 진행하며, 필요시 열교환기 프로그램을 이용하여 simulation mode에서 현재 운전상태를 verify하여 의사결정에 도움을 줄 수 있다.
근본적 원인을 찾기 위해 site visit, 공정 변수 기록, 운전상태 관찰 혹은 infrared thermal reading을 통해 thermal distribution에 대한 진단을 할 수 있다. 그리고 정기 보수기간에 bundle을 꺼내어 내부를 검사하여 fouling상태 확인, fouling층의 두께 측정 및 분석, 부식이나 진동으로 인한 두께 감소부분 확인, tube leak test를 실시하고 필요시 leak된 tube는 plugging한다.
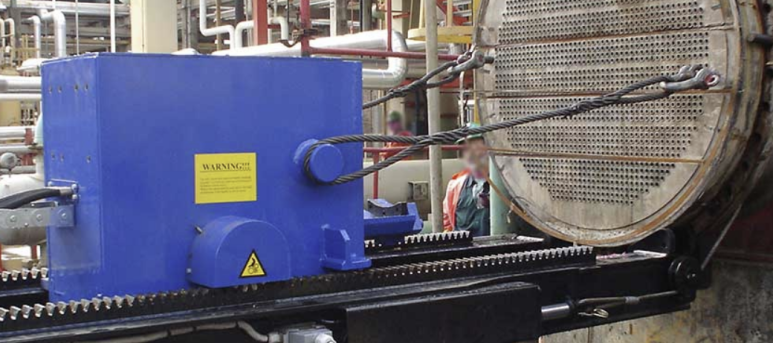
bundle pull out
이처럼 Troubleshooting의 첫 단계가 바로 inspection에 대한 자료이며 이를 이용하여 현재 운전상태를 진단하는 것이다. 검사 결과를 가지고 언제 어떤 방법으로 청소하고 수리하고 교체할 지를 결정하되 문제점을 인지하고 검사 결과를 포함한 정보들을 수집하고 분석한 후 원인 및 이에 대한 대책을 마련하여 실행을 한다. 검사에는 육안검사로서 먼저 tube내부를 flashlight나 fiber optic scope을 이용하여 check하고 ultrasonic 방법으로 자세히 check한다. 비파괴 검사를 위해 bundle을 빼내고 tube를 분리하여 검사를 한다.
경험적으로 보면 Start-up시의 trouble은 주로 설계오류에 기인하며, 운전중 trouble은 주로 fouling이나 진동 등의 급격한 진행 및 설계치를 벗어난 운전조건에 대부분 원인이 있다.
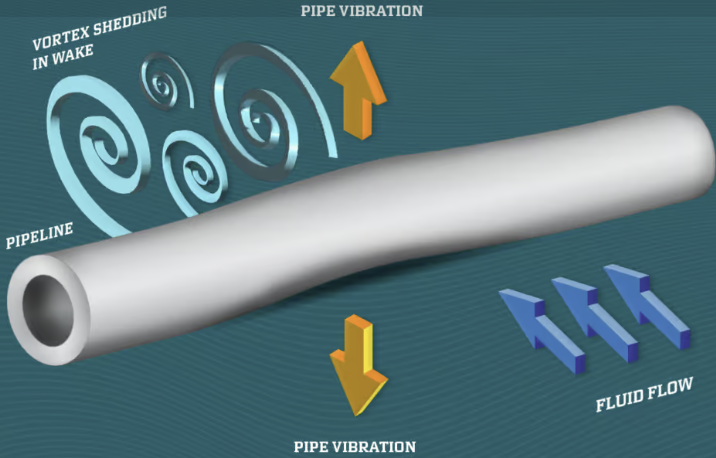
열교환기와 관련된 주요 문제로는 아래와 같이 크게 3가지로 나누어 볼 수 있다. 먼저 Structural problem으로는 FIV (Flow Induced Vibration)으로 인한 failure와 bolted joint로부터의 leakage이며 유체 도입에 따른 진동으로 vortex shedding, turbulent buffeting, fluidelastic coupling의 형태에 의해 증폭되어 tube에 damage를 주는 경우이며, 두 번째로는 Performance problem으로 지나친 tube fouling과 열교환기 내부에서의 thermal stress에 따라 성능 저하 및 기계적 문제를 야기한다. 마지막으로 Metallurgical problem으로는 stress corrosion, galvanic corrosion, erosion등이 있다.
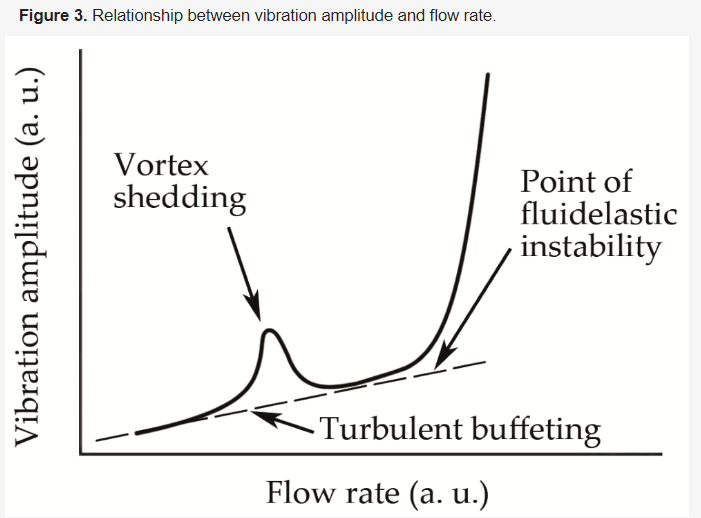
Pitting은 SCC (Stress Corrosion Cracking) 현상의 가장 흔한 종류이며, 알루미늄과 SS가 SCC에 가장 취약하고, pitting부식은 국부적인 것으로서 metal surface에 구멍이 생기는 것으로 general corrosion에 비해 penetration이 10~100배에 이른다. Failure analysis를 진행할 때 부식과 관련해서는 부식의 종류, 부식율, 부식과 다른 failure mechanism과의 상호작용의 factor들을 고려해야 한다.
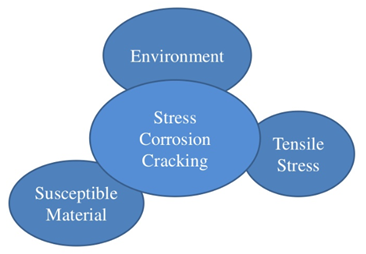
다양한 원인만큼이나 개선책도 다양하겠지만 크게 보면 critical한 경우 performance issue, 운전 trouble와 관련하여 운전비가 증가될 수 있고 초기에 해결하지 못할 경우 그로 인한 영향으로 기계적 변경이나 재설계를 해야 할 수도 있다. troubleshooting의 경험에 기초한 주요 문제점들로는 진동문제, 열교환기 leakage, 에너지 소비 증가, Pass partition bypassing (thermal leakage), Fouling and scaling 등으로 파악하고 있다.
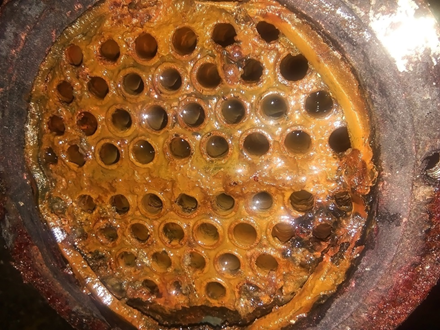
Fouling issue
유체마다 각기 다른 특성에 따라 오염계수도 다르며 운전중 열교환기 성능에 가장 큰 영향을 주는 요인이기도 하다. 때로는 성능감소 외에도 큰 압력손실까지 야기하여 공장 전체적으로 performance에 영향을 줄 수도 있다. 따라서 cleaning을 위해 운전기간 단축 및 fouling 원인 규명 및 공정 운전조건에 변화를 주어 해결해야 하지만 효과적인 방법은 못되고, shut down후 cleaning을 하되 추후 spare 열교환기를 고려하여 on stream시간을 늘려야 한다.
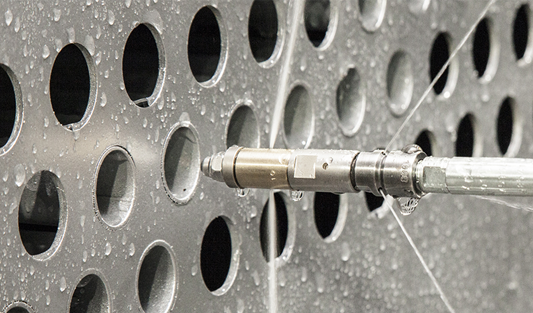
정상운전간에 이물질이나 scale이 열전달 표면에 build up되어 열전달을 방해함에 따라 열교환기 전후단의 온도 변화 및 유량, 압력변화를 관찰하면서 Fouling과 scaling의 진행상황을 예상할 수 있다.
파울링은 열전달 표면에 dirt, slime, scale이 build up되는 것을 말하며 침강, 결정화, 부식, 고분자화 등이 파울링의 주요 원인이다. 특히 냉각수를 사용하는 열교환기의 경우 파울링 문제를 해결하고자 back flushing system을 고려한다. 반면 스케일링은 온도 감소에 따라 용해도가 낮아져 석출되거나, 혼합물내 유체들 사이의 화학반응이나 부식에 의해 발생되는 파울링의 한 형태이다.
파울링은 여러 형태에 의해 발생됨에 따라 적절한 resolution을 얻기 위해서는 fouling mechanism과 fouling type에 대해 확신이 있어야 한다. 또한 특정 파울링은 일반적이지 않아 특정 공정에서만 나타날 수도 있다. Fouling의 type으로는 결정화, 분해, 고분자화, 산화, 슬러지나 녹 더스트 입자의 침강, 생물학적 퇴적, 부식등이다.
Fouling은 유체 종류와 열전달 공정에 따라 type을 결정할 수 있다. 예를 들어 생물학적 퇴적에 따른 파울링은 냉각수 배관상에 적절한 filter를 설치 및 particulate 제거를 통해 성능을 개선할 수 있다.
하지만 대부분 파울링은 열전달과 관련이 되어 특히 고온 유체에 따른 고분자화나 분해가 파울링를 더 심각하게 한다. 따라서 공정 성능상 문제가 없는 범위 내에서 단순히 온도만 낮추어도 파울링 진행 속도를 크게 낮출 수 있어서 cleaning의 빈도를 줄일 수 있다.
fouling이나 scaling을 방지하기 위해서는 dirty fluid에 대해 열교환기 전단에 filter를 고려하거나 주기적으로 열교환기를 청소해야 한다. 물로 인해 야기되는 scale은 대부분 mineral을 함유한 hard water가 열교환기를 통과해 가면서 scale이 tube 표면에 deposit되며 특히 유속이 느릴 경우 심해진다. 따라서 mineral을 제거하기 위해 ion exchange와 같은 softening treatment를 설치하거나 scale을 방지하기 위해 chemical treatment를 고려할 수 있다.
이러한 활동들은 deposit을 완벽히 방지하는 개념이 아니라 deposit되는 속도를 최대한 늦추는 것이 목적이며 유속이 느리면 Particle이 suspension 상태를 유지하지 못하고 열전단 표면에 settling되어 고온의 표면에서 석출될 수 있다. 따라서 가능하면 dirty fluid를 tube side에 배열하여 높은 유속을 유지함을 통해 fouling을 최소화할 수 있고 tube side cleaning도 용이해진다.
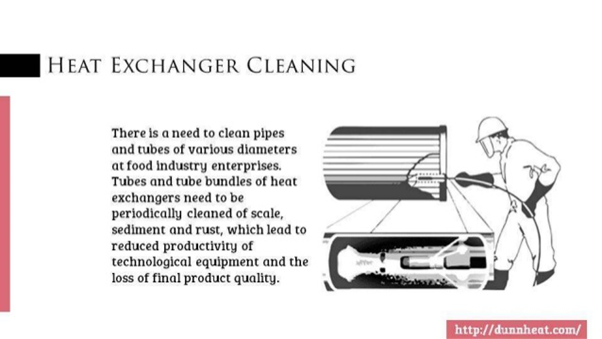
Particulate fouling은 유체내 부유 입자가 tube 표면으로 누적되는 것을 말하며 corrosion fouling은 tube 재질들의 반응에 의해 생성된 부식물질들이 tube표면에 석출되는 현상이다. 박테리아나 균류, 해조류등이 열전달 표면에 붙어 생물학적 파울링이 일어날 수 있다. Fouling의 결과로 유지비용과 환경 관리 비용이 증가될 수 있다.
Manual cleaning으로는 equipment내부에 cleaning solution을 채워 펌프로 circulation을 하며 이 때 농도와 온도변화를 관찰한다.
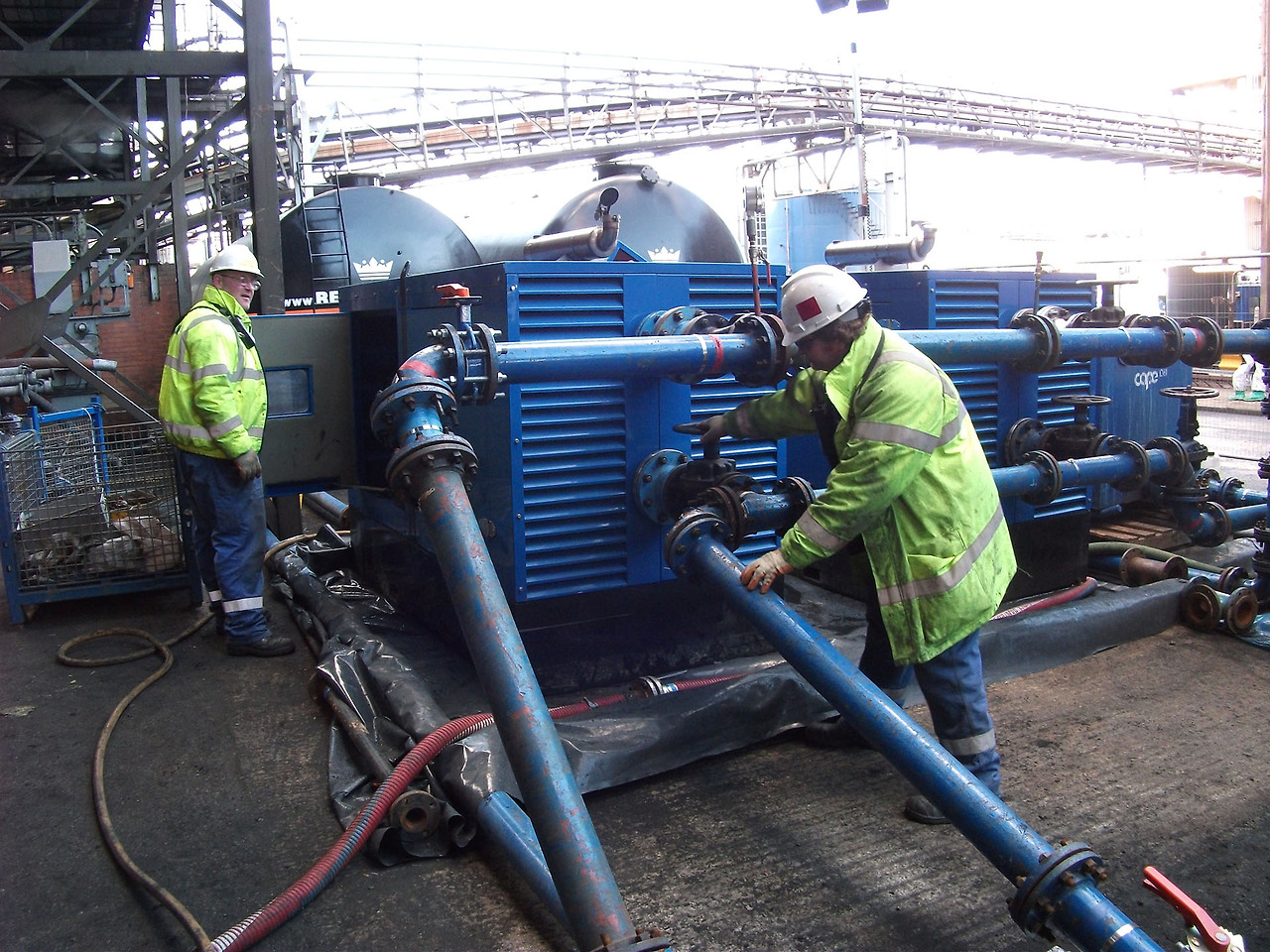
하지만 매우 작은 equipment인 경우 circulation 대신 채우고 soaking하고 나서 비우는 작업을 반복하여 만족한 결과를 얻을 수 있다. 장점으로는 청소를 완벽히 할 수 있고 가끔 chemical cleaning만이 유일한 방법일 수 있으며 access하기 어려운 곳에도 청소를 할 수 있으며, 청소 비용이 적절하고 청소주기를 늘릴 수 있다. 단점으로는 사용되는 chemical들이 보통은 위험물질이며 환경친화적이지 않다.
Online cleaning방법의 Flow excursion은 fouling deposit을 제거하기 위해 일시적으로 유량을 늘리며 이 방법은 유속이 느려 발생되는 fouling에 적용된다. 다른 방법으로 air bumping이 있으며 air slug를 만들어 국부적 난류에 따라 fouling을 제거한다. Automatic tube cleaning system을 적용하여 냉각수 안에 sponge rubber ball을 함께 넣어 tube를 통해 deposit된 물질들을 제거한다.
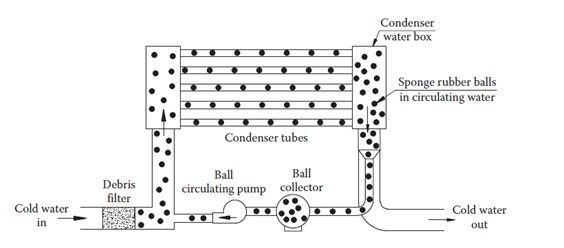
장점으로는 설치하기가 용이하고 plant shut down을 할 필요가 없으며 시간과 노동력을 줄일 수 있지만 단점으로는 경우에 따라 초기 투자비가 클 수 있다.
열교환기 leak
대기로 leak되는 것은 쉽게 확인이 되지만 내부에서의 leak는 분명치가 않아 지속적인 공정 변수의 모니터링과 sampling을 통해 관리되어야 한다. 정기보수시 TEMA type에 따라 가능한 type인 경우 한쪽 끝의 tube를 막고 반대쪽에서 가압하여 압력을 유지하는지에 따라 leak 여부를 판단할 수 있다. 혹은 형광물질의 염료를 이용하여 leak 여부를 확인할 수도 있다.
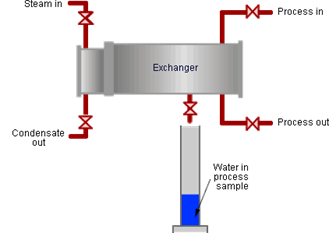
Tube leaks는 tube 마모나 손상, 부식에 의해 발생되며, 정기보수시 검사나 운전중 sampling분석을 통해 확인이 되며, 안전상의 문제로는 고압측의 압력이 저압측에 영향을 줄 수 있어서 과압의 가능성을 검토해야 한다. Repair나 bundle 교체 전까지는 임시적으로 leak tube를 plugging을 하여 운전을 할 수 있지만 이로 인한 전열면적의 감소는 고려해야 한다.
Steam inefficiency
열원으로 스팀을 사용시 운전중 유량이나 온도, 압력의 변화가 있다면 이는 대부분 condensate 제거가 원활하지 않아 발생되는 경우이다. 이 경우 steam trap 운전상태를 check하거나 condensate piping routing을 확인해야 한다.
그 밖에 주요 운전상 문제 및 원인들로는 입출구 온도차가 설계 대비 낮을 경우 scale이나 fouling이 원인일 수 있으며, 입출구 압력차가 설계 대비 클 경우 fouling이 더 심해졌거나 blockage가 원인일 수 있다. outlet압력이 감소하는 것은 leak의 가능성이 있으며 inlet 압력이 감소한 것은 upstream 시스템 압력 감소나 inlet 배관상 valve가 닫혔을 가능성이 있다.
원하는 온도로 접근하지 않을 경우 대부분 전열면적이 부족하여 발생되는 것으로 이는 설계과정에서 기본 data가 잘못되었거나 운전과정에서 공정조건이 변하여 발생된 것이다. 이 때 성능 개선을 위해 냉각매체나 열원의 유량을 늘려볼 수도 있지만 한계가 있으므로 추후 열교환기를 교체하거나 series 혹은 parallel로 설치를 검토해야 한다.
부적절한 노즐 위치 및 impingement plate, baffle의 잘못된 설계나 제작 등이 원인이 될 수 있고 two phase흐름의 경우 열교환기 내부에서 상분리가 될 수 있어서 불균일한 유량 분배의 가능성이 매우 높다. 아울러 점도가 큰 유체가 tube side로 흐를 시 각각의 tube를 통한 온도차가 미세하게 달라 더 많이 냉각된 tube를 통해 나오는 유체의 점도가 더 커지고 이에 따라 차압이 더 많이 걸려서 상대적으로 다른 tube보다 유량이 더 적게 흐른다. (점도가 높을 경우 가급적 shell side로 고려한다.) 제작도면을 검토하여 흐름에 장애를 유발하는 요인이 있는지 확인하고 정기보수 검사시 각 tube 내부 상태를 확인하여 plugging이 된 tube에 대해 검토하여 원인을 유추해 본다.
열교환기는 보통 governing case 및 fouling을 염두하여 설계를 하며, 여기에 spec기준, 10%이상 overdesign을 요구함에 따라 start-up시 fouling이 없는 clean상태 및 초기 turn down유량으로 운전시에 설계된 열교환기는 필요 면적보다 과도한 전열면적을 제공하게 되어, 특히 냉각수의 경우 필요로 하는 냉각수 유량은 더욱 줄어 유속이 급격히 떨어지고 이 때 fouling등이 심하게 발생하여 이후 정상조건에서는 오히려 열전달 효율의 저하를 야기할 수 있다. overdesign문제가 지속적으로 문제가 된다면 flow arrangement를 Counter current에서 co current로 변경하거나 일부 tube를 unplugging할 수 있다.
reboiler와 condenser의 운전상 문제점 및 이에 대한 대응 방법은 다음과 같다.
Reboiler 운전시 문제점
boiling fluid가 이물질이나 용존 고체를 함유하고 있다면 boiling과정에서 고체의 농축은 증가하여 용해도를 초과시 고체는 뜨거운 tube 표면에 침착하여 Fouling 및 부식이나 coking등을 야기한다.
Thermosiphon reboiler return line size가 적절하지 않아 너무 작게 설계될 경우 flow가 불안정하고 과도한 차압으로 인해 circulation유량이 적어지고 vapor fraction이 많아져 이로 인한 flow induced vibration을 야기할 수 있으며, boiling 유체의 압력이 증가함에 따라 포화온도도 증가하여 양측의 온도차가 줄고 열전달 속도도 줄어들어 vapor발생은 매우 줄어들 수도 있다. 이 경우 column운전에 영향을 주게 되므로 일정 load 이상 운전이 불가능해진다. 반대로 return line size가 너무 크게 설계할 경우 수평배관에서 층이 형성되어 liquid가 reboiler로 다시 역류되어 heavy한 성분들이 reboiler내에 축척될 수 있다.
Thermosiphon reboiler는 film boiling, dryout, flow instability에 의해 제약을 받는다. Tube wall에서 heat flux가 과도하게 일어난다면 hot surface에서 vapor가 제거되는 속도보다 생성되는 속도가 빨라 tube는 vapor로 film이 형성되어 열전달 속도가 급격히 줄게 된다. 유입 액체가 과도하게 증발이 일어나면 tube wall이 wet상태가 아니라 dry 상태가 되며 비증발 액체는 vapor와 함께 흘러가는 mist flow가 되며 이 때의 열전달 계수는 급격히 줄어들게 되므로 증발되는 vapor분율은 0.2~0.3정도를 유지해야 한다. 순환 유량이 설계대비 매우 높거나 vapor fraction이 매우 클 경우 return line에서의 flow instability가 일어날 수 있다.
Kettle reboiler의 경우 시운전시에 정상상태의 bottom조성보다 boiling point가 낮을 수 있어서 stream이 bundle로 유입시 많은 양의 vapor가 발생되어 tube damage를 줄 수 있으므로 이러한 경우를 대비하여 reboiler inlet line에 valve를 고려하여 throttling을 하면서 load-up을 해야 한다. Kettle reboiler bundle이 클 경우 top과 bottom의 압력차에 의한 온도변화를 설계시에 반영해야 한다. Liquid 혼합물이 boiling이 될 경우 tube방향에 따라 길이가 길 경우 조성 변화가 일어날 수 있어서 가능하면 feed nozzle을 2개 이상 고려하여 유입되게 한다.
Shell 직경이 충분히 크게 설계되지 않으면 발생된 증기가 나가면서 일부 액체가 딸려 나갈 수 있으므로 설계시에 이를 감안해야 하며, 특히 진공운전일 경우 주의를 해야 한다. 아울러 bundle내에서 liquid/vapor 유속이 크거나 bundle이 적절하게 지지를 받지 못하면 진동문제가 생길 수 있다. 따라서 feed nozzle은 충분히 크게 설계하여 RhoV2가 1500lb/ft2s보다 작도록 하고 U tube의 경우 U bend부위가 취약하므로 support baffle을 고려해야 한다.
Condenser 운전시 문제점
냉각수의 fouling이 가장 흔하게 발생될 수 있어서 tube side내 유속 유지가 매우 중요하며 process의 경우 크게 문제되지는 않지만 간혹 응축되면서 고형화가 일어나는 공정이 있음에 따라 process 특성을 감안하여 설계단계에서 이를 고려해야 한다.
Condensate 배출에 문제가 되어 flooding이 발생될 수 있으며 이에 대한 원인 파악을 위해, 배출 배관의 구성 및 size가 적절한지 확인 및 압력 계기를 이용하여 압력 profile을 검토해 본다.
Condenser는 잠재적으로 inert gas가 누적될 수 있는 설비임에 따라 total condenser의 경우 condenser rear head부분에 vent를 할 수 있도록 고려해야 한다. Inert gas가 누적될 경우 응축성분의 분압이 줄어들어 결국 포화온도도 낮아짐에 따라 응축이 잘 안될 수 있으며, inert gas 존재로 열전달 계수가 급격히 줄며, 이용 가능한 전열면적도 줄어들게 되어 performance에 크게 영향을 준다.
Shell 이나 tube내에서 inert gas가 pocket을 형성할 경우 흐름을 block할 수 있고 shell side내 upper tube들을 blanket하여 열전달을 방해하여 열교환기 입출구 온도차가 감소하거나 국부적 hot spot을 야기할 수도 있다. 이 경우 venting을 하여 inert gas를 제거해야 한다.
아래는 troubleshooting의 경험에 기반한 원인 및 대책에 대한 list이며 이를 통해 주요 문제점 및 대응책을 확인할 수 있다.
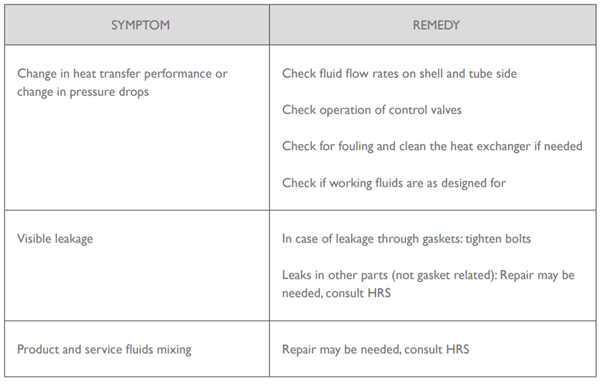
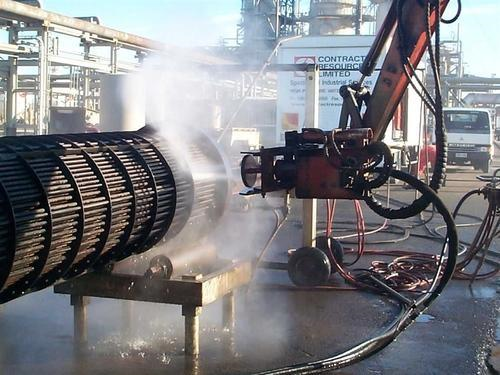
Operational Problem
|
Possible Causes
|
Action
|
High outlet temperature
|
· Low flow of coolant so heat transfer is reduced
· Build up of scale reduces heat transfer
· Coolant inlet temperature too high
|
· Fully open coolant inlet valve
· Boost coolant pump rpm
· Remove scale
· Send coolant to cooling tower
|
Low outlet temperature
|
· Excessive heat transfer when coolant flow is too high
· Excessive heat transfer when coolant inlet temperature is too low
|
· Throttle coolant inlet valve
· Reduce coolant pump rpm
· Reduce chilling of coolant
|
Small temperature difference between inlet and outlet
|
· Poor heat transfer due to low coolant fluid flow
· Scale build up in exchanger reduces heat transfer through pipe walls
· Coolant fluid inlet temperature too high so less heat is transferred
|
· Fully open coolant inlet valve
· Boost coolant pump rpm
· Remove scale
· Send coolant to cooling tower
|
High outlet pressure
|
· Incorrect valve lineup or equipment downstream of the outlet restricts the flow
|
· Check SOP for lineup
· Check downstream bottleneck
|
Low outlet pressure (with high inlet pressure)
|
· Blockage in the exchanger reduces flow at the outlet
|
· Inspect and service to clear blockage
|
High inlet pressure
|
· Incorrect valve lineup or equipment downstream of the outlet restricts the flow
· Blockage in the exchanger reduces flow
· Blockage downstream from the exchanger reduces flow
|
· Check SOP for lineup
· Check downstream bottleneck
· Inspect and service to clear blockage
|
Low inlet pressure
|
· Incorrect valve lineup or equipment upstream of the inlet restricts inlet flow
· Blockage upstream from inlet restricts flow at the inlet
|
· Check SOP for lineup
· Check upstream bottleneck
· Inspect and service to clear blockage
|
Large pressure difference between inlet and outlet
|
· Blockage in the exchanger produces high pressure on the inlet side and low pressure on the outlet side
|
· Inspect and service to clear blockage
|
'화학공장 troubleshooting' 카테고리의 다른 글
증류탑내 trapped component의 최소화 (0) | 2025.01.15 |
---|---|
증류탑 bottleneck troubleshooting (0) | 2025.01.04 |
troubleshooting 사례 (0) | 2024.12.28 |
pump troubleshooting (0) | 2024.12.28 |
Deaerator flooding (0) | 2024.12.28 |