열교환기 설계순서
공정설계 과정의 전체적인 heat and material balance를 통해 열교환기 설계를 위한 공정 조건 및 물성치를 확정한다.
이후 열교환기 설계는 기본설계와 상세설계로 나뉘며, 기본설계는 heat duty와 pressure drop을 만족하는 크기와 재질을 확정하고, 이를 기초로 온도, 압력, 기타 힘에 견디는 두께, 치수를 결정하는 상세설계로 진행이 된다.
기본설계 절차로는 먼저 설계요구자료를 확인하여 공정 data, 물성치 및 spec상 요구조건을 토대로 필요 열량을 계산하고 shell, tube 및 baffle에 대한 형상, 치수 및 개수등을 가정한다. 이후 stream analysis를 검토하고 관외측과 내측의 경막계수를 계산한다.
이를 통해 총괄 열전달계수를 계산하고 평균 온도차와 실제 열량을 계산하여 over design 만족 여부를 확인하여 만족하지 못할 경우 형상이나 치수를 조정하여 다시 반복한다. Over design을 만족한다면 이제는 관외측과 내측에 대해 압력손실을 계산하여 allowable값을 만족하지 못하면 다시 형상과 치수를 조정하고, 만족하면 flow induced vibration을 check한다. 진동이 기준치를 초과하면 다시 형상이나 치수, baffle 간격 등을 조정하고 만족하면 계산을 종료한다.
설계요구자료는 최소한 각 side의 입구와 출구의 온도, 압력 및 유량, fouling factor와 물성치인 밀도, 점도, 열전도도와 비열이 필요하다. 상이 변하는 경우 bubble point, dew point 및 heat release curve가 제공되어야 하며 특히 reboiler의 경우 임계온도, 임계압력, 표면장력이 필요하다.
아울러 증류탑 내부의 액체 높이에 따른 reboiler inlet nozzle 압력에서의 포화온도와의 관계를 위해 다양한 압력에서의 heat curve가 필요하다. (주로 HLL, NLL, LLL에서의 압력기준) 그리고 maintenance 및 운반을 위해 최대 shell 직경과 bundle 크기가 결정되어야 하며 유체 오염 특성에 따른 cleaning을 감안한 tube layout도 define이 되어야 한다.
Overall heat transfer coefficient (US)
Total fouling factor값이 0.003이고, allowable pressure drop이 5~10psi인 경우 경험적인 수치는 다음과 같다.
cooler
Hot fluid
|
Cold fluid
|
Overall U
|
Water
|
water
|
250~500
|
Methanol
|
water
|
250~500
|
Ammonia
|
water
|
250~500
|
Aqueous solution
|
water
|
250~500
|
Light organic
|
water
|
75~150
|
Medium organic
|
water
|
50~125
|
Heavy organic
|
water
|
5~75
|
Gas
|
water
|
2~50
|
Water
|
Brine
|
100~200
|
Light organic
|
briner
|
40~100
|
heater
Hot fluid
|
Cold fluid
|
Overall U
|
steam
|
water
|
200~700
|
steam
|
Methanol
|
200~700
|
steam
|
Ammonia
|
200~700
|
steam
|
Less than 2cP
|
200~700
|
steam
|
More than 2cP
|
100~500
|
steam
|
Light organic
|
100~200
|
steam
|
Medium organic
|
50~100
|
steam
|
Heavy organic
|
6~60
|
steam
|
gas
|
5~50
|
exchanger
Hot fluid
|
Cold fluid
|
Overall U
|
water
|
water
|
250~500
|
Aqueous solution
|
Aqueous solution
|
250~500
|
Light organic
|
Light organic
|
10~75
|
Medium organic
|
Medium organic
|
20~60
|
Heavy organic
|
Heavy organic
|
10~60
|
Light organic은 점도가 0.5cP이하이고 벤젠, 톨루엔, 아세톤, 에탄올, 메틸케톤, 가솔린, 라이트 케로진, 납사 등을 말하며 medium organic은 점도가 0.5~1cP로서 케로진, 크루드를 말하고 heavy organic은 점도가 1cP이상으로 윤활유, fuel oil, CDU/VDU bottoms, tars, asphalt등을 의미한다.
열교환기의 형태
Front head
A type은 channel이나 배관의 분리없이 tube 내부 청소가 가능하도록 channel cover 분리가 되는 구조로 비싸지만 널리 사용되며, B type은 channel이 bonnet로 되어 분리가 불가한 구조이며 tube측 유체의 누출을 막아야 할 경우에 적용하고 아울러 fouling factor가 0.0004m2Ch/kcal이하에 적용한다. C type은 front end의 tubesheet가 channel과 일체형의 구조를 갖고 있으며, N type은 tubesheet, channel, shell이 일체형으로 되어 있어서 shell side cleaning이 불가하므로 깨끗한 유체를 서비스해야 하며, D type은 channel 전체가 단조 구조로서 고압 (150bar이상)에서 사용하는 구조이다.
선택기준으로 안전성, 신뢰성, 유지관리 용이성, 비용면에서 고려를 하되 tube side유체의 leak를 방지하기 위해서는 C나 N type을 적용하고, tube side압력이 매우 높은 경우 D type을 적용하며 tube side유체가 dirty할 경우 A type을 적용하고, 경제성을 고려한다면 B type을 선정한다.
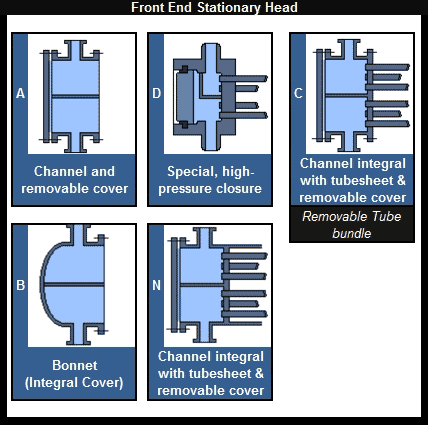
Rear head
L type은 A type과 유사하고, M type은 B type과 유사하다. N type은 front head의 N type과 같다. S type은 floating으로서 shell cover와 floating head assembly를 분해해야 bundle을 빼낼 수 있는 구조이며 T type은 tube side가 고압인 경우에 적용하고, floating head assembly를 해체하지 않고도 bundle인출이 가능한 구조이다. U type은 U tube를 사용한 구조이다.
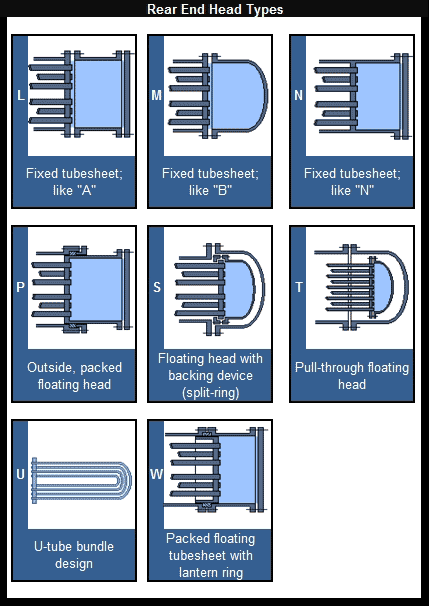
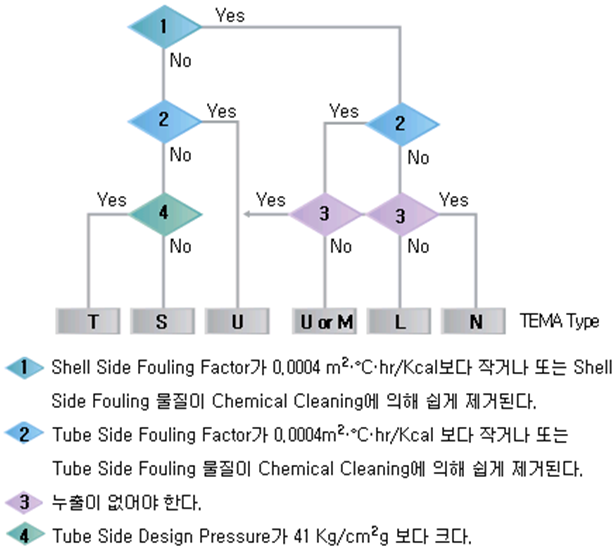
즉, shell side가 비교적 깨끗하면 B, M type을, 더러우면 S,T type을 적용하고 tube side가 비교적 깨끗하면 B, M, U type을, 더러우면 A, L type을 고려한다.
Shell type
E type: 가장 많이 사용되며 shell side 입구, 출구가 각각 1개이며 shell pass도 하나임. 열전달 효과 및 압력손실이 큼.
F type: shell 내부에 longitudinal baffle이 설치되어 shell pass가 2pass가 되며 이 baffle을 통한 thermal leakage를 고려하여 insulated baffle을 적용하지만, 실제 산업용으로는 잘 적용하지는 않는다. 압력손실은 E shell의 약 8배 정도로 매우 크며, close temperature approach나 low shell side flow rate때문에 E shell은 쓸 수 없고, 2개의 shell을 series로 사용해야 할 경우 고려할 수 있다.
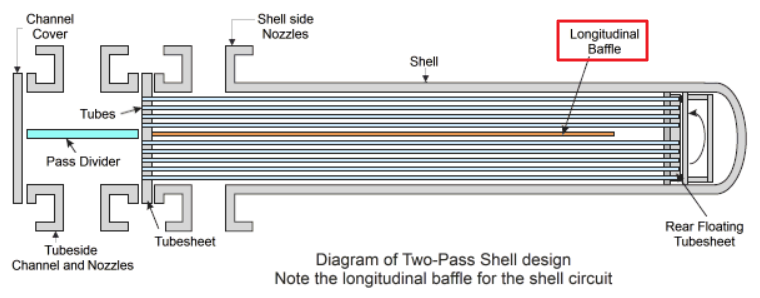
G type: split flow로서 shell side흐름이 양분되어 차압은 E shell과 비슷하나 열효율이 좋으며 shellside thermosiphon에 많이 사용됨.
H type: double split flow로서 G type보다 차압이 더 적고 열전달 효과도 더 낮음. shellside thermosiphon에 많이 사용됨.
J type: J12 or J21의 divided flow로 inlet이 하나이며 outlet이 2개이거나, inlet이 2개이며 outlet이 하나인 형태로서 E type에 비해 shellside 차압을 1/8정도로 크게 줄인 반면 열전달 효과도 감소하게 됨. 주로 저압의 gas cooler에 적용함.
K type: pool boiling목적으로 사용되며, 증류탑의 부하나 level변화에 민감한 thermosiphon과 달리 증류탑의 변화에 관계없이 안정된 운전을 할 수 있음.
X type: shell side흐름이 tube side흐름과 수직방향인 cross flow형태로서 위로 올라가며 shell side 유속이 매우 낮고 압력손실도 매우 낮아 열전달효과도 낮다. Shell side흐름이 shell 길이에 대해 균일하게 흐르도록 내부에 distributor를 설치할 수 있다.
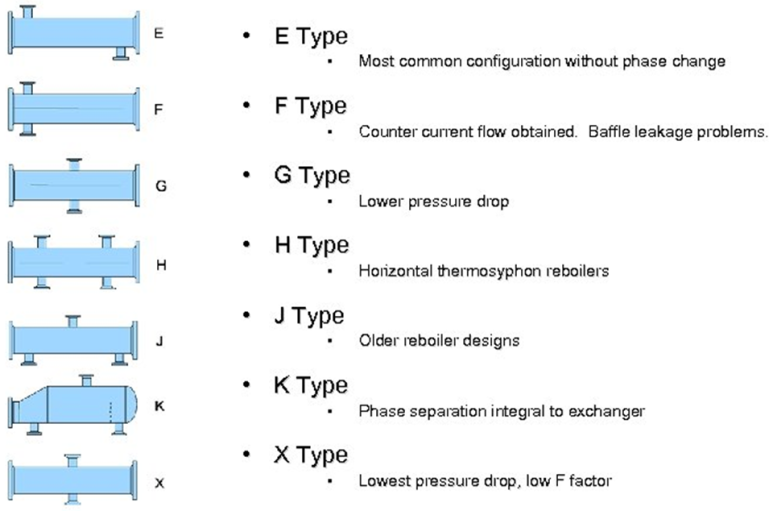
전열관
길이는 일반적으로 8, 10, 12, 16, 20ft를 사용하지만 프로젝트에 따라 다를 수 있으며, tube 두께는 BWG (BWG 수치와 두께는 반비례 관계)에 따라 적용하되 thickness tolerance는 min인지 average인지 언급이 되어야 하며, 부식여유는 고려하지 않는다. 주어진 전열면적에 대해 tube길이가 길수록 열교환기 가격이 낮아진다.
3/4”미만의 tube는 cleaning하기가 어렵고, 차압이 많이 걸릴 경우 1 1/2”이상을 고려한다. Tube side 설계압력이 높을 경우 tube 두께가 과도하지 않도록 더 작은 tube size를 선호한다. Tube는 교체 대상임에 따라 부식 여유는 고려하지 않으며, 유체 자체가 매우 부식적이라면 tube wall 두께를 키운다. Tube 두께는 min 혹은 average로 define하되, 평균 두께로 지정한 것이 더 싸다. 고압이 아니거나 부식적이지 않을 경우 보통 평균 두께를 의미한다.
아래 표는 code에서 허용하는 stress에 따른 tube가 견딜 수 있는 최대 압력을 보여주며 3/4”, BWG12의 경우 최대 6,578psi (450 bar)까지 견딜 수 있다. 이러한 이유로 고압의 경우 경제성을 고려하여 shell side보다는 tube side에 우선적으로 배치를 하게 된다. 아울러 small diameter가 더 높은 압력에 견디므로 가능한 3/4” OD를 고려한다. tube는 1/2"~2" 범위중 보통 3/4"OD, 1"OD를 많이 적용한다.
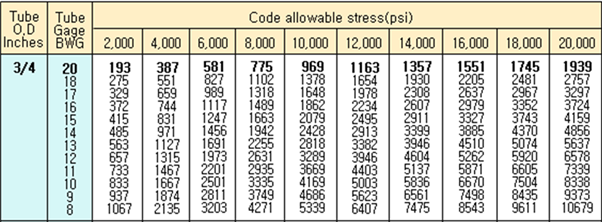
bare tube 전열면적을 키우기 위해 fin을 사용할 수도 있으며 rear head쪽의 channel 대신 U tube를 사용할 수도 있다. tube내부에 열전달 효과를 키우기 위해 twisted tape을 사용할 수 있지만 fouling이 심하거나 freezing경향이 있을 경우 사용이 제한된다.
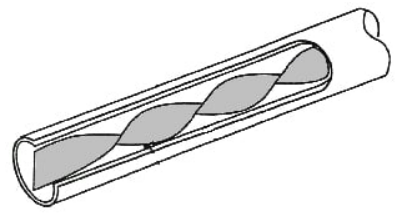
tube pattern은 30, 45, 60, 90도가 있으며 깨끗한 유체인 경우 30도를 많이 적용하고 주어진 shell diameter에 대해 가장 많은 tube을 설치할 수 있으며, pressure drop이 크고 열전달 효과도 좋아 특별한 고려사항이 없으면 우선적으로 적용하며 (60도는 압력손실 대비 열전달 효과가 낮기 때문에 잘 사용하지 않음), mechanical cleaning이 필요할 경우 45도나 90도 pattern을 적용한다.
triangular configuratino은 square pattern에 비해 5~10% tube가 더 많이 들어가지만 그만큼 shell side (tube 밖) 청소가 어렵다. shell side cleaning이 필요하다면 square pattern이나 tube pitch를 크게 한다. 이러한 배경으로 fixed tube sheet는 triangular 배치를 하여 chemical cleaning을 하고, 반면 U tube나 floating head인 경우 square pattern을 고려한다.
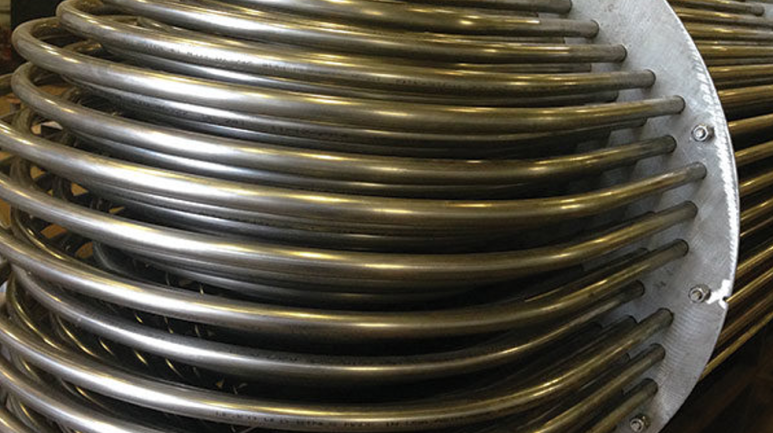
square와 rotated square pitch 차이는 shell side의 turbulence정도에 의존하여, 점성이 높은 유체인 경우 난류 정도가 매우 낮아 이 때는 rotated square pattern을 적용하여 동일한 차압에 대해 더 높은 열전달 효율을 제공한다. 열교환기 청소를 위해 chemical / mechanical 방법 여부에 따라 pitch 선정에 영향을 준다.
reboiler와 같이 shell side에서 vapor를 발생시키는 경우에는 침전물을 방지하기 위해 90도를 선택한다. shell side가 층류일 경우에는 90도를 피하고 난류일 때는 열전달 효율이 높고 pressure drop은 낮다. 아울러 45도 layout은 열전달이 잘 되며, 30도 layout에 비해 85%정도의 tube를 설치할 수 있다.
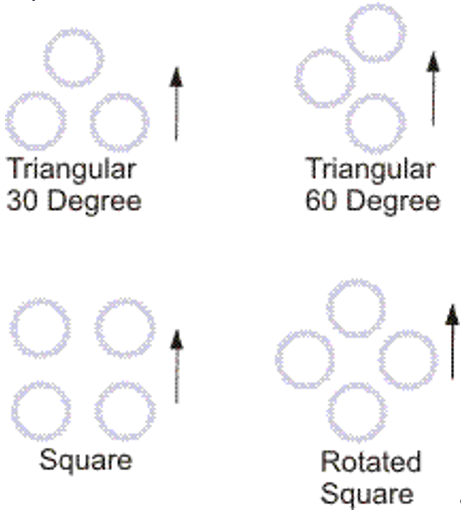
Tube pitch는 인접한 tube 중심선 사이의 가장 짧은 거리를 말하며 일반적으로 OD의 최소 1.25배 (tube clearance는 0.25배), 최대 1.5배를 적용하고, mechanical cleaning을 해야 할 경우 pitch 간격은 이를 충분히 고려해야 한다. tube spacing은 tube diameter에 대한 tube pitch의 비율로서 보통 1.25~1.33를 적용하며, mechanical cleaning 목적의 square layout tube들 사이의 최소 gap은 6.35mm가 필요하다. 기계적 청소 목적이나 tube end welding을 위해 더 큰 pitch를 요구하지 않는다면 보통 tube pitch는 1.25를 적용한다.
열교환기 내부 구조물
Baffle: 유로를 형성하여 유속 증가 및 난류를 만들고 진동을 방지하며 tube를 지지하는 목적이 있음. longitudinal baffle과 cross baffle이 있는데 보통 baffle이라 칭할 때에는 일반적으로는 cross baffle을 의미하여 tube 흐름과 shell 흐름이 직각으로 흘러 열전달이 잘 이루어지도록 하기 위함이며 모양상으로 single segmental, double segmental, NTIW (No Tube In Window)으로 구분하고, 이는 shell side pressure drop과 FIV에 의해 결정하며, cut위치에 따라 vertical baffle과 horizontal baffle 그리고 많이 사용되지는 않지만 rotated baffle로 나눈다. Baffle cut중 horizontal의 경우 단일 유체에 적합하며, 2phase일 경우 부적합하고 shell side유체가 dirty할 경우 baffle아랫부분에 settling의 가능성이 있다. 반면 vertical cut는 phase에 무관하게 dirty성분에서도 사용할 수 있다.
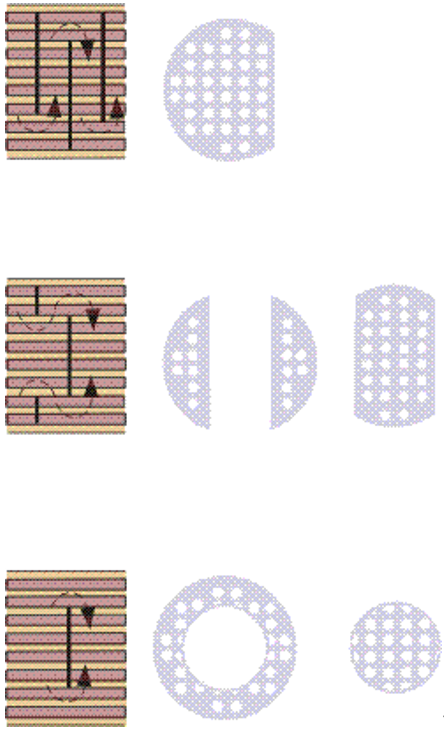
Baffle이 plate가 아닌 rod 형태의 rod baffle도 있다. Baffle은 shell에 용접된 게 아니고 baffle내 hole 역시 tube와의 clearance가 있어서 이를 통한 leakage가 있음에 따라 sizing을 수행시 각 stream별 leakage %를 확인후 baffle span을 조절하여 performance를 개선할 수 있다. 최소 baffle span은 shell diameter의 20% 혹은 최소 2”이상이며 shell diameter보다는 작아야 한다. TEMA에는 maximum unsupported span을 define하여 재질별, tube OD별 규정을 하고 있다.
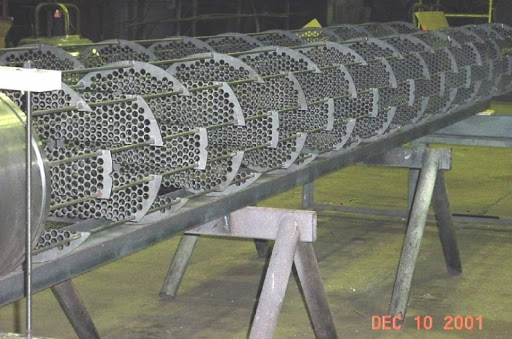
baffle cut는 shell diameter에 대한 baffle cutting height의 비율로서 보통은 20~30%이며 너무 작거나 크면 열전단 효율이 감소한다. 아울러 baffle cut는 baffle pitch와 비교하여 baffle window를 통한 유속이 tube의 crossflow의 유속과 비슷하도록 dimension을 고려한다. baffle cut는 baffle type에 따라 다르며 single segmental일 경우 보통 45%, double segmental일 경우 25%를 적용한다. 액체인 경우 baffle cut는 shell 직경의 20~25%이며, 가스는 더 낮은 차압이 요구되므로 baffle cut는 shell 직경의 40~45%를 차지한다. tube support를 위해 적어도 하나의 tube row는 overlap이 되어야 한다.
baffle간의 간격을 baffle pitch라고 하며 이는 shell side crossflow 유속과 tube support, pressure drop을 변경하기 위해 조절한다. TEMA에서는 baffle pitch에 대한 최소~최대 값을 제공한다.
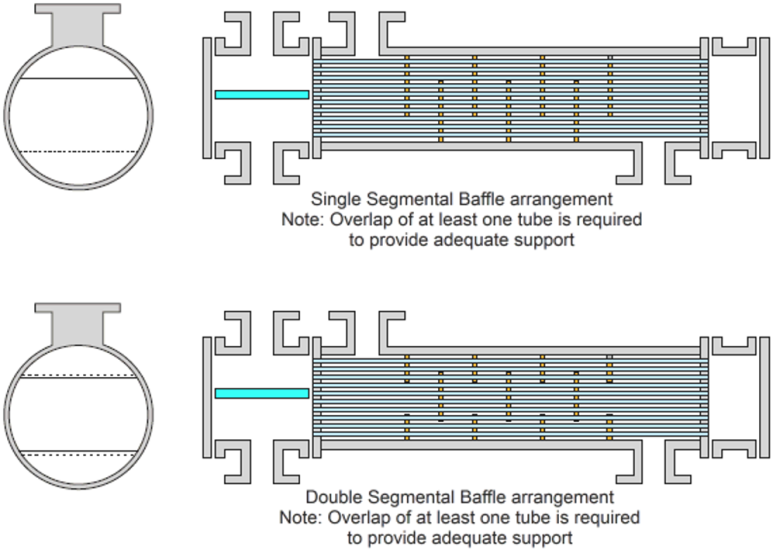
Single segment baffle에 비해 double segment baffle은 shell side 유속이 절반으로 줄며 따라서 차압도 single에 비해 1/4로 줄어 열전달 효율도 크게 줄어들 수 있어서, 차압이 critical하게 문제가 되지 않는다면 single segment baffle을 적용한다.
Tie rod and spacer: baffle을 지지하기 위해 설치되는 rod로서 한쪽은 tubesheet에 고정하고 다른 쪽은 마지막 baffle이나 support plate 외곽에 고정하며, rod외부에 baffle사이 간격을 유지하도록 spacer도 설치된다.
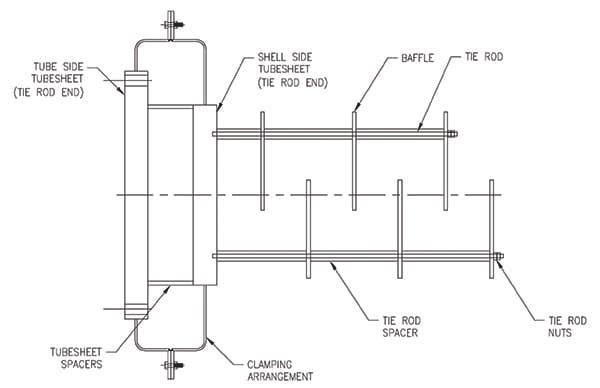
Intermediate Support plate: tube vibration 및 tube 자체의 무게를 고려하여 일정 길이마다 tube를 지지하기 위해 고려하며 baffle로 불충분할 경우 그 사이에 삽입하며, 주로 NTIW, X shell 및 U bend에 국한하고 floating block의 무게를 지지하기 위해 floating tubesheet 근처에도 설치할 수 있다.
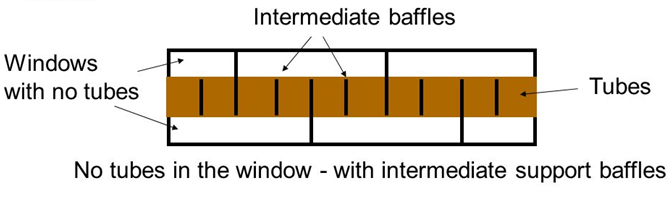
Sealing device: sealing strip과 seal rod가 있으며 bundle과 shell사이의 clearance사이로 흐르는 bypass를 줄이기 위해 sealing strip을 고려하고, multi tube pass인 경우 pass partition lane을 따라 bypassing하는 F stream을 줄이기 위해 seal rod 혹은 dummy pipe를 설치한다. 일반적으로 최외각 tube와 shell의 간극이 tube pitch의 1/2을 초과시 설치하지만 thermal rating과정에서 program이 필요시 자동적으로 결정하고 그 반영된 결과를 보여준다. 임의로 설치할 경우 오히려 pressure drop만 유발하고 열전달에 도움을 주지 않을 수도 있고 특히 응축이나 증발하는 열교환기에서는 seal strip설치는 열전달에 거의 영향을 주지 않으므로 고려하지 않는다.
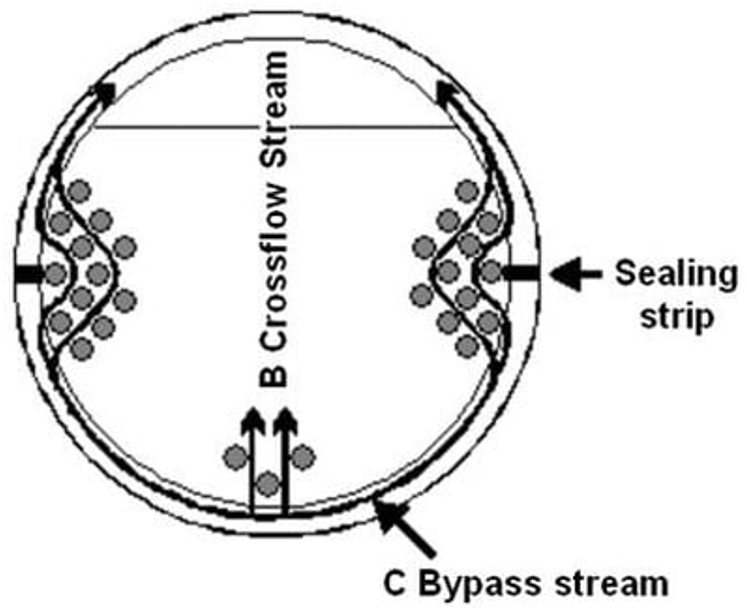
Pass partition plate: multi tube pass일 경우 channel내부에 설치하여 tube side의 pass수를 유지해준다.
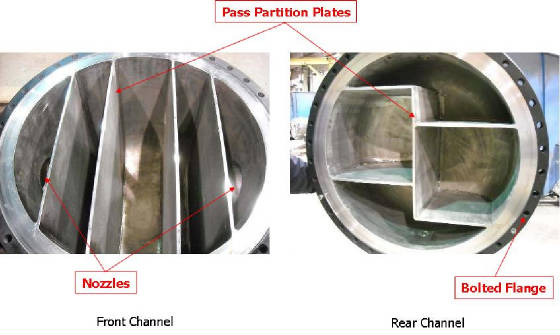
tube pass는 보통 1, 혹은 짝수를 적용하며, tube pass를 증가시키면 열전달이 커지지만, tube side ρv2가 10,000 kg/m·s2를 초과하지 않도록 주의해야 한다.
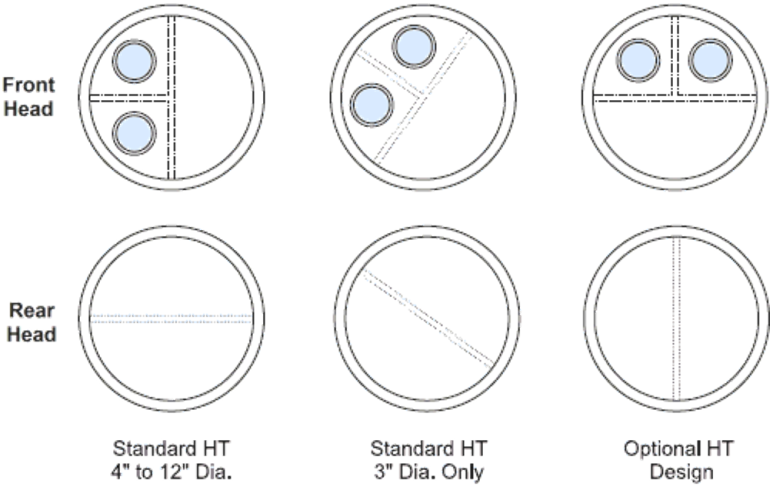
4 pass tube side design
Impingement plate: 노즐을 통해 shell에 유입되는 유체의 속도가 빠를 경우 erosion이나 flow induced vibration으로 인해 tube damage가 발생할 수 있어서 flow가 직접 bundle에 충격을 주지 않도록 plate를 설치하되 그 기준은 TEMA에 따른다. 계산은 impact factor를 의미하는 물리량인 ρv2를 이용하여 TEMA 기준치와 비교하여 impingement protection plate여부를 결정한다.
Nozzle diameter에서의 속도가 큰 경우 impingement plate를 설치하여 들어오는 유체를 tube로 잘 분산시키고 vibration, erosion을 방지한다. Impingement plate를 설치함에 따라 shell 내에 설치될 tube가 줄어들지만 shell 상부에 dome을 설치하면 tube를 full로 설치할 수 있다.
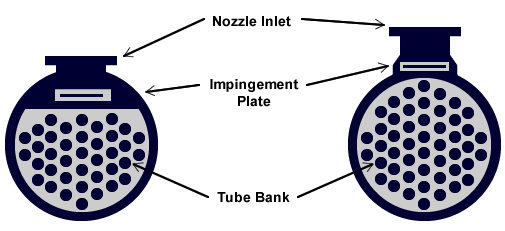
일반적으로 corrosive / abrasive / erosive gas 및 포화증기 또는 2phase인 경우 impingement plate가 항상 필요하며 그외 부식 또는 마모성의 액체인 경우 ρv2가 740kg/ms2 초과할 경우, 부식성이 없거나 마모성이 없는 single phase 유체에 대해서는 ρv2가 2,230kg/ms2 초과할 경우 impingement plate를 설치한다. 아울러 shell, bundle entrance, exit area의 ρv2가 5,950kg/ms2을 초과해서는 안된다. shell side nozzle에 대해서는 ρv2가 9,000 kg/m·s2을 초과해서는 안된다.
circular 혹은 rectangular plate가 보통 적용해왔지만, impingement rod가 FIV를 최소화할 수 있어서 이제는 이 type을 많이 사용되고 있다.
Detuning baffle (de-resonating baffle): acoustic vibration문제를 해결하기 위한 방법으로 shell 유체가 가스나 2phase일 경우 유속과 shell diameter에 따라 소음 진동 문제가 될 수 있으며, 이 때 baffle과 직각이며 shell 유체 흐름에 평행하게 longitudinal baffle을 설치한다.
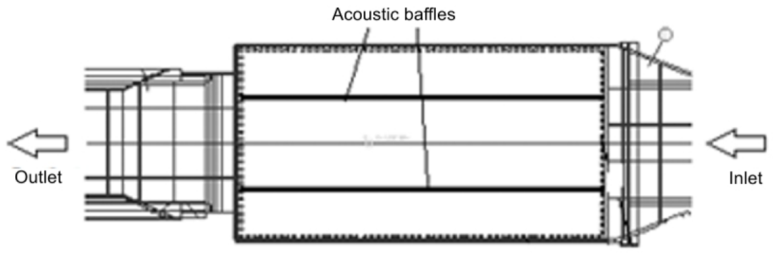
Tubesheet joint: heavy expanding이 기본이며 여기에 leak tightness를 위해 seal weld를 부가할 수 있다. 또 다른 tube to tubesheet joint로는 strength welding이 있으며 여기에 부가적으로 light expanding을 고려할 수도 있으며 이는 project spec에 따라 적용해야 한다.
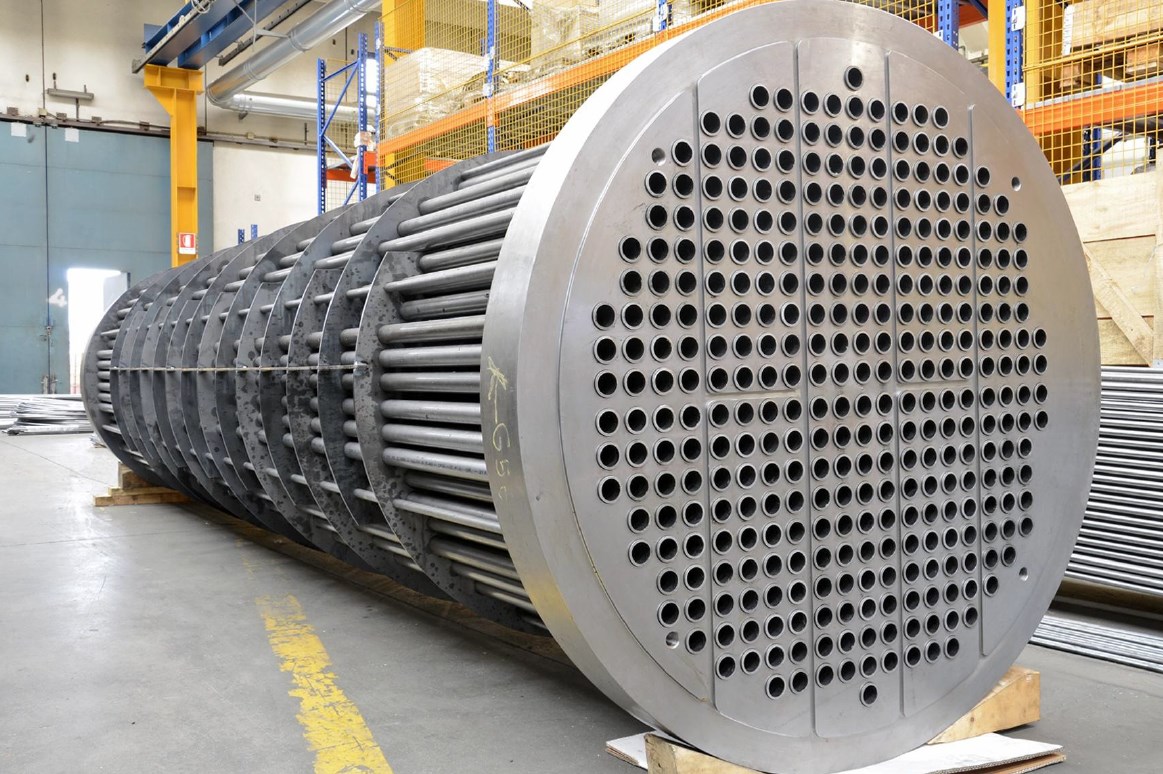
Tube sheet는 양측 유체와 contact하므로 재질이나 부식 여유 선정에 고려해야 한다. 비싼 Solid alloy 재질 대신 CS에 alloy bonding하여 부식 저항성을 키울 수 있다.
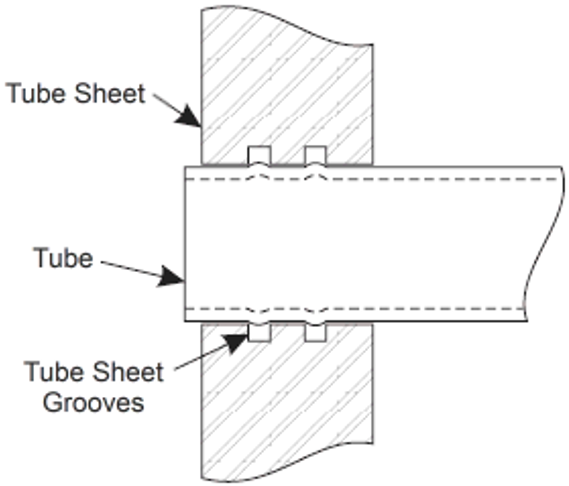
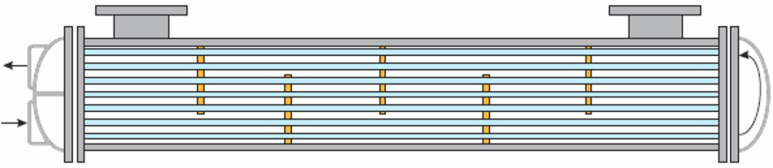
shell 직경이 24”까지는 pipe를 이용하며 그 이상은 rolled plate를 적용하지만 이 경우 roundness가 issue이다. 특히 24”이하는 배관으로 만들어서 비용이 저렴하고, 완전한 원 모양임에 따라 제작이 용이하다. 둥글지 않으면 shell side내 bypass stream을 야기할 수 있다.
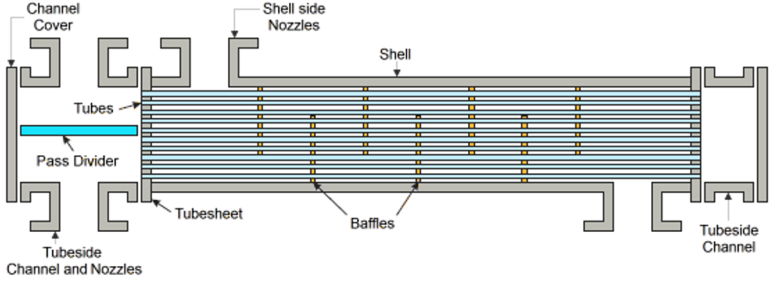
Annular distributor (vapor belt): shell 입구, 출구에 baffle space간격이 좁아 차압이 많이 걸리거나 flow induced vibration이 우려될 경우 shell외부에 enclosure를 설치하여 shell opening을 통해 유입되도록 한다.
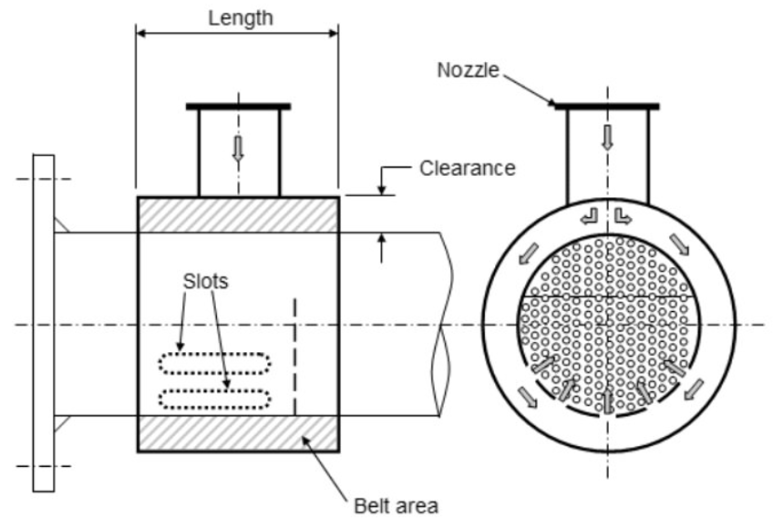
Tubing
주로 크기는 5/8” ~ 1 1/2”이며, shell side 유체의 열전달계수가 tube side보다 크게 낮을 경우 finned tubing을 적용하고, 특히 U tube는 U-bend부분에서 청소하기가 어렵고 bundle 내부 튜브들은 교체하기도 어려워 단순히 plugging만 한다.
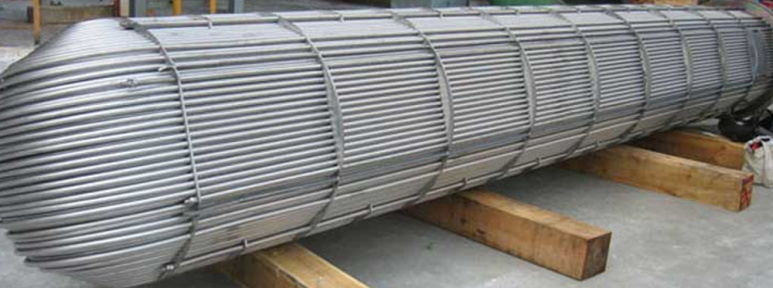
열교환기 설치 형태
상변화가 없는 경우 유체가 흐르는 방향이 자연대류 방향과 같은 방향인지, 역방향인지에 따라 열전달 계수 차이가 미미하지만 기본적으로 저온측이 아래부분, 고온측이 윗부분에 연결을 하며, maintenance 및 layout를 고려하여 설치한다.
상변화가 있는 경우 응축 혹은 비등시 설치 방향에 따른 특징 및 장단점, 열전달계수와 압력 손실에 차이가 있음에 따라 공정 목적에 맞게 설치되어야 하며 이는 plot결정에 top priority가 되어야 한다.
유체의 위치선정 (fluid allocation)
가장 중요한 것은 safety와 reliability이며, 절대적인 기준은 아니지만 유체의 특성이나 운전조건을 감안, tube side로 냉각수, 부식성 유체, 침전물 유체, fouling유체, 점도가 작은 유체, 고온이나 고압 유체를 우선적으로 고려하며 주요 인자들은 다음과 같다.
일반적으로 CW는 빠른 유속을 유지하기 위해 보통 tube side에 배치를 하지만, flammable이나 toxic 유체일 경우 tube side에 배치를 한다. 따라서 CW를 tube side로 할 지 shell side로 할 지는 pressure rating, 부식성, process유체의 fouling등에 영향을 받는다.
허용 차압이 낮을 경우 shell side에 고려하고, one pass당 온도차이가 큰 stream의 경우 shell side에 배치하여 axial compression tension을 줄이고 expansion joint를 피할 수 있다.
Bundle이 fixed일 경우 shell side로 access가 어려워 mechanical cleaning이 불가하여 chemical cleaning밖에 할 수 없어서 가급적 dirty fluid일 경우 tube side로 배치하는 것이 좋다. 특히 shell side로 CW가 흐를 때 52도가 넘을 경우 water내 이물질 및 salt 등이 tube 겉표면에 석출되어 열전달 성능 및 maintenance에 문제를 야기할 수 있어서 CW outlet 온도는 가급적 48도를 넘지 말아야 한다.
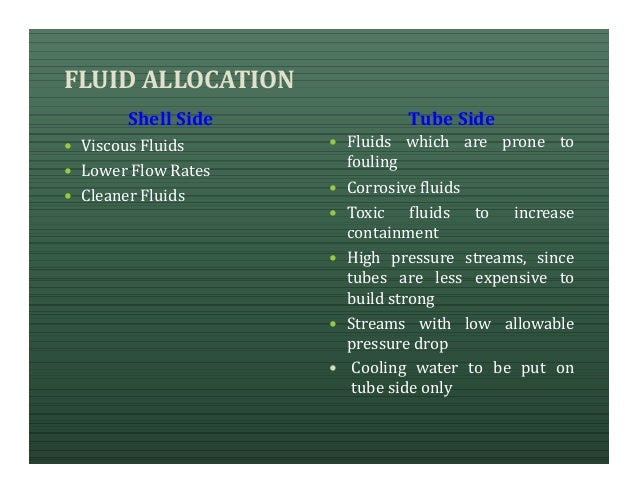
운전압력: 고압 유체를 tube로 흐르게 하여 경제적 설계를 한다.
부식성: 부식성이 강한 유체를 tube로 흐르게 하여 tube만 high grade로 선정한다.
오염 및 청소: fouling이 큰 유체는 청소가 용이하도록 tube로 흐르게 하며 chemical cleaning이 가능할 경우에는 shell측에 흐를 수도 있다. Tube의 기계적 청소가 요구될 경우에는 직관을 사용하고, shell측에 기계적 청소를 할 경우 tube pitch나 layout을 크게 고려해야 하므로 결국 장치가 커질 수 있다.
점도: 고점도 유체를 shell측에 흘러 baffle을 통해 난류를 형성하여 높은 열전달을 이룰 수 있지만, 유속이 낮은 층류이거나 finned tube일 경우에는 tube측으로 전환한다.
허용 압력손실: 허용 압력손실이 클수록 tube로 흐르게 한다. 하지만 층류 흐름일 경우 유체가 난류가 되도록 shell측으로 고려한다. 만약 충분한 압력손실을 적용하기 위해 multi tube pass를 적용시 차압이 초과할 경우에는 오히려 tube가 아닌 shell측에 적용하되 baffle span을 조정해본다. 특히 shell측에 허용 압력손실이 큰 유체를 흘러 보낼 경우 tube vibration문제를 check해야 한다.
압력손실 이용성: tube측의 경우 관직경과 길이가 일정하다면 tube pass를 1에서 N으로 변경시 압력손실은 N^3배로 증가하여 너무 크게 변경이 됨에 따라 trial & error과정에서 관직경과 길이를 다시 변경해야 한다. 반면 shell의 경우 허용 압력손실을 최대한 이용하기 위해 shell type, baffle spacing, tube layout, tube pitch등을 조절하여 허용 압력손실을 극대화할 수 있다.
예외적으로 응축되는 증기는 shell side로 하고, 다만 스팀의 경우 tube side로 통과시킨다. 그리고 열 팽창과 열 응력을 최소화하기 위해 입/출구에서 온도변화가 큰 유체 (300 ~ 350F이상)는 shell side로 통과시킨다.
Prandtl No는 열적 경계층 두께 (온도 profile)에 대한 유체역학적 경계층의 두께 (속도 profile)의 비를 말하며 이 값이 1보다 아주 작을 경우 속도의 영향을 거의 받지 않고 전도율만 영향을 받게 된다는 의미이다.
Shell 개수
Temperature cross가 허용되기 위해서는 F factor값이 0.8 이상 되어야 한다. 그렇지 못할 경우 shell을 series로 추가해야 한다. 보통은 계단작도를 이용하여 양측 온도가 cross되는 부분에 대해 shell 개수를 부여한다.
반면 process heat load가 매우 커서 TEMA에서 규정한 최대 크기 및 maintenance 측면, 운송 측면에서 허용 크기를 초과시에는 stream을 2개 이상으로 나누어 parallel로 설치해야 한다. 다만 제작비 및 설치 공간 측면을 고려하여 가능한 나누지 않는 방향으로 검토가 되어야 한다.
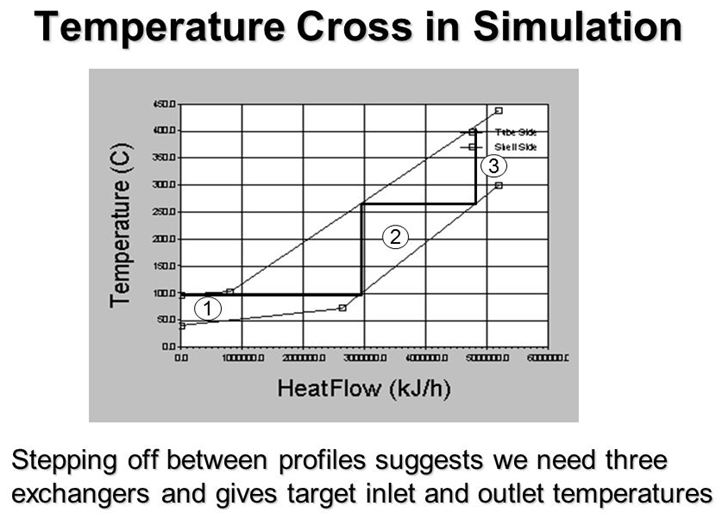
Tube pass가 2 이상일 경우 pure counter current flow는 불가능해져 LMTD는 correction해야 하며, 보통 F factor를 이용하여 cocurrent, countercurrent에 대한 보상을 한다.
shell 직경은 610mm (24")까지 표준 배관을 적용하며, 이보다 클 경우 rolled plate를 적용한다. shell diameter는 보통 152mm~3,000mm (6" to 120")를 적용한다. 다만, shell 직경이 200mm이하일 경우 hairpin heat exchanger가 좋은 선택이 되며 아울러 500kW이하의 low heat duty에 대해서도 hairpin을 고려한다.
Nozzle size
일반적으로 배관 size와 동일하지만 열교환기에 허용되는 pressure drop을 기준했을 때 nozzle에서의 차압이 매우 클 경우 nozzle size를 키워야 한다.
특히 shell side의 nozzle은 shell diameter의 1/3을 초과하지 않도록 하며, 일반적으로 RhoV2가 9,000kg/ms2을 초과하지 않도록 sizing한다.
Fouling factor
Reboiler와 같은 경우 boiling과정에서 vapor가 발생되고 남은 찌꺼기가 tube벽면에 달라붙어 큰 오염저항으로 작용할 수 있다. Fouling factor는 매우 중요하지만 이론적으로 계산하기에는 어려운 값으로 보통은 경험적인 값을 사용한다.
재질 두께 선정시 설계조건을 기준으로 계산적으로 나온 두께에 추가하여 부식여유를 더해주는 것처럼 열교환기 sizing시에 이론적으로 계산된 열전달 계수에 오염 저항을 고려하여 열전달 계수를 조정해야 한다. 그렇지 않으면 과도하게 설계하거나 너무 작게 설계하여 제 성능이 나오지 않을 수도 있다.
Fouling의 특징으로 HC은 냉각될 때보다 가열될 때 더 심하며, boiling되는 열교환기는 과포화 영역에서 잔유물의 응집이 더 심하며 반면 속도가 빠를수록 오염을 방지한다. 오염의 형태로는 precipitation fouling, particulate fouling, chemical reaction fouling, corrosion fouling, biological fouling이 있다.
유체의 종류에 따라 fouling정도가 다르며 온도에 비례하여 fouling경향이 나타나고 (예를 들어 냉각수의 경우 return온도가 50도를 넘으면 무기물이 침전될 수 있다.) 속도에 비례하여 fouling경향이 감소한다. 하지만 tube의 유속은 erosion에 의해 제한되며 shell의 경우 FIV에 의해 제한되므로 이 기준을 맞추되 가급적 빠른 유속을 유지해야 한다.
Fouling 경향이 높은 유체는 tube side로 배치하여 청소가 용이하게 하고 운전중 정체구간의 최소화 및 유속을 일정하게 유지할 수 있다.
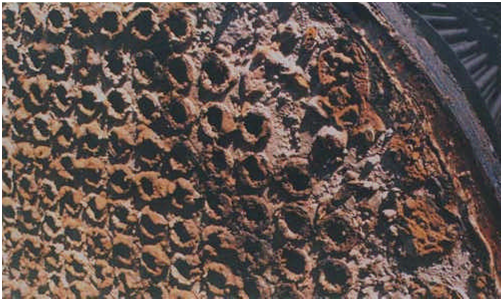
열전달 효율을 개선할 수 있는 방법들로는 아래와 같이 3가지를 고려해 볼 수 있다.
special surface: temperature driving force가 작을 때 핵비등을 개선하기 위해 고려
tube insert: wire wound insert나 twisted tape으로서, 이는 주로 점도가 높은 경우 난류를 만들어 열전달을 개선하기 위해 적용하며 fouling을 줄여주는 역할도 한다.
extended surface: stream의 열전달계수가 낮을 때 전열면적을 키우기 위해 적용하며, 가장 흔한 type이 low fin tubing으로서 핀 높이는 1.5mm이고 inch당 19개 fin이 설치된다.
재질은 보통 metal계열을 사용하지만 강산이나 의약 제조 분야에는 graphite, plastic, glass를 적용하기도 한다.
#fouling#FIV#U#TEMA#baffle#BWG#tie_rod#sealing_strip#vapor_belt#allocation#temperature_cross#insert#low_fin#rod_baffle#tie_rod#spacer# acoustic_vibration# vapor_belt# allocation#핵비등
'열교환기 설계' 카테고리의 다른 글
propylene vaporizer rating (0) | 2024.12.20 |
---|---|
kettle type steam vaporizer sizing (0) | 2024.12.19 |
열교환기 분류 (0) | 2024.12.19 |
열교환기 개요 (1) | 2024.12.19 |
hairpin exchanger (0) | 2024.12.15 |