cryogenic plant의 가장 critical issue중 하나가 수분의 동결 등 freezing이나 hydrate 생성으로 인한 trouble이다. 따라서 초기 start-up시에 dryout activity가 매우 중요하다. 하지만 중요도에 비해 관심은 그에 미치지 못한 것이 현실이며, 프로젝트 진행중에 설계에 고려해야 할 사항들이 있음에도 간과할 경우 추후 현장에서 start-up이 지연될 수 밖에 없다.
수분을 제거해야 한다는 것은 아는데, dryout동안 얼마나 많은 수분이 제거되었는지, dryout이 끝났을 때 확신할 수 있는지 등 start-up동안 면밀히 고려해야 한다.
HC내 수분이 존재할 경우 생기는 solid는 ice가 아니라 hydrate로 알려진 결정 구조이다. hydrate는 물의 freezing point 이상의 온도 조건에서 생성될 수 있다. 수분이 충분히 존재하고 저온 및 고압의 조건에서 hydrate는 쉽게 생기며 이 의미는 cold plant의 start-up동안 온도를 낮추는 과정에서 충분한 수분이 있을 경우 hydrate가 발생되어 배관이나 열교환기, strainer, filter, 혹은 계기의 tubing line을 막을 수 있어서 이로 인해 shut down을 야기하게 된다.
아울러 thermosyphon reboiler나 side heater에 hydrate가 생기면 흐름이 감소되어 결국 column에 공급되어야 할 열량이 충분하지 않아 off spec의 가능성이 크게 된다. 그리고 column내 tray나 packing에도 영향을 주어 분리 효율 감소로 product recovery가 줄거나 off spec이 될 수 있다. 뿐만 아니라 control valve의 plugging도 hydrate로 인한 주요 trouble 결과이다.
수분은 공사단계에서의 대기 open배관을 통해 빗물 유입이나 대기중 수분의 응축을 통해 process내부에 존재할 수 있고, hydrostatic test를 위해 채워진 물의 일부가 emptying이후 남아 있을 수도 있다. 그래서 cold plant의 start-up전에 가장 중요한 단계가 배관이나 시스템으로부터 가능한 free water를 blow out해야 한다. 정량적 측면에서 수 ppm 단위의 수분으로 낮추어야 안전하고 효율적으로 cold plant를 운전할 수 있다.
low point를 통해 drain만 한다고 해서 모든 물들이 제거되는 것은 아니며 vapor 상태의 수분 흡수를 하여 dryout 요구조건을 맞추어야 한다. 이를 위해 잔여 수분을 제거하기 위한 몇가지 option들이 있다. 이는 현장 상황에 맞도록 비용이나 스케쥴, 장단점을 파악하여 최적의 cooldown 절차를 적용해야 한다.
Option 1
cold plant의 section을 나누고 isolation후 질소를 이용하여 가압, 감압을 반복하여 cycling하면서 수분을 제거한다. 이는 별도의 specific 배관 설계를 요구하지 않고, 단지 low point drain위치를 적절히 선정하고 개수가 충분해야 하며 drain size도 적절해야 한다. 하지만 이 방법을 적용하기 위해서는 많은 양의 질소가 소비되므로 충분한 양을 확보해야 하며 따라서 system내 물이 많이 존재한다면 이 방법이 현실적이지 않을 수 있다.
아울러 질소 퍼지 이후 잔여 수분의 양을 assume하기 쉽지 않고 다른 방법에 비해 모든 수분이 허용 기준 이하로 제거되었는지 확신하기가 어렵다. 잔여 수분의 정확한 양에 대한 정보를 얻기 위해 많은 point에서 water content reading을 해야 한다.
Option 2
once through 방법으로 hot, dehydrated gas를 주입하여 flare stack이나 다른 곳에 reinjection하는 방법으로 진행할 수 있다. dryout path는 가능한 낮은 압력에서 운전하고, system을 통한 차압은 최소화를 하여 drying시 process를 cool down할 수 있는 Joule-Thomson (J-T) expansion을 피한다. 이 방법을 적용하기 위해서는 적절한 유량이 흘러야 free water가 low point로 이동하거나 water vapor를 absorbing할 수 있다. system의 drying 압력을 낮추기 위해 orifice나 valve와 같은 device를 설치한다.
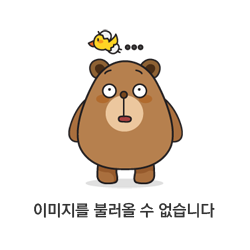
하지만 이 방법을 적용시 flare stack이나 reinjection system의 capacity이하에서 drying 유량이 유지되어야 하지만, 매우 효율적인 방법임에 따라 많은 프로젝트에서 적용되어 왔다. 다만, 원하는 수분의 양 이내로 유지하기 위해 drying시간이 지연될 수는 있다.
Option 3
closed loop로서 once through와 유사하지만 cold plant를 통해 나오는 가스를 compressor를 이용하여 응축시킨 후 다시 inlet gas로 재사용하는 concept이다.
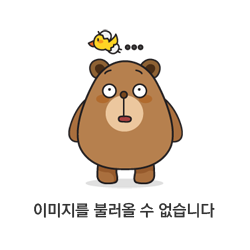
이 방법 역시 compressor shut down없이 가능한 낮은 압력에서 drying운전을 하며 system을 통한 차압은 최소화를 하여 drying시 process를 cool down할 수 있는 Joule-Thomson (J-T) expansion을 피한다. 차압은 최소화하지만 system을 통한 유량은 충분히 확보하여 free water가 low point로 이동하고, water vapor를 absorbing후, 후단의 air cooler에서 제거할 수 있다. 이 방법 역시 once through와 유사하게 system의 drying 압력을 낮추기 위해 orifice나 valve와 같은 device를 전단에 설치한다. 이 방법이 짧은 시간에 drying을 하므로 가장 추천하며, 또한 앞서 기술된 pressure cycling이나 excess flaring처럼 과도한 질소가 소모되는 것이 아니다.
N2 pressure cycling방법은 대기중 응축된 수분을 제거할 경우에는 효과적이지만 free water를 low point로 이동시켜 제거하기에는 적절하지 않다. once through dryout option은 cold plant를 통한 wet dryout gas를 배출하기 위한 적절한 위치를 고려해야 하며, closed loop를 통한 dryout progress를 모니터링하는 것이 상대적으로 용이하며, dryout이후 cooldown으로의 전이도 매우 빠르게 진행될 수 있고 fresh gas feed-in전에 recirculation gas를 이용하여 cooldown을 미리 진행할 수도 있다.
따라서 이러한 dryout option에 대해 상세설계단계에서 충분히 검토하여 설계에 반영해야 하며 dryout action전에 procedure를 준비하여 전 staff이 일관된 방향으로 dryout을 수행할 수 있다.
Cold plant design features
비록 아래 언급된 설계요소들이 dryout을 위해 필요하지만 alternative로서도 이용될 수 있다. 예를 들어 maintenance나 repair전에 공정 설비를 isolation 및 설비로부터 HC을 venting하고, dehydrator 후단에서 water content를 모니터링한다. 설계적 측면에서 recirculation piping, pressure reducing device와 위치, drain valve설치, stagnent process area를 설정하고 performance확인을 위한 water content 측정 위치도 설계단계에서 충분히 검토 및 고려되어야 한다.
Recirculation piping
closed loop를 완성하기 위해 아래와 같이 bypass 배관을 고려한다.
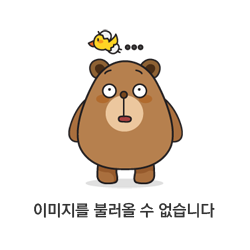
Pressure-reducing device and location
dryout을 위한 감압용 device위치는 dehydrator 재생시스템의 설계와 재생 가스의 source에 의존한다.

예를 들어 재생을 위한 inlet gas를 사용시 compressor에서 과도한 head가 요구되어 pressure reducing device는 location1에 설치하지 않는다. 만약 temporary orice를 location2에 설치한다면 아래와 같이 dust filter와 후단 밸브사이의 flange에 설치할 수 있다. spare filter가 있어서 언제든지 교체 및 철거가 가능하다.
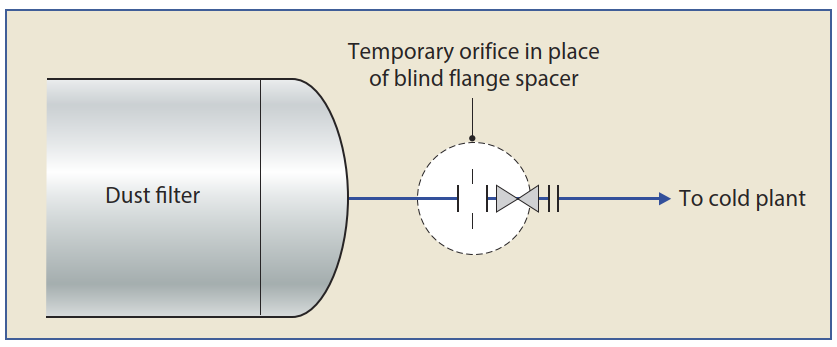
특히 35bar 이상의 차압이 매우 큰 경우에 대비해 orifice plate 두께는 충분히 고려되어야 하며 dryout을 위한 허용되는 유량이 흐르도록 sizing이 되어야 하고, 특히 cold plant J-T valve가 약 2bar의 차압에서 full open되어 흐르는 최대 유량을 cover해야 한다. 경험적으로 보면 dryout유량은 full through 유량의 약 30% 정도가 되며 이 때, compressor운전은 surge를 피하도록 적절히 설계 및 운전되어야 하며 이를 위해 surge control valve가 dryout case에 대해 설계되어야 한다.
Drain valve
3D model review동안 주요 저온 설비 주변의 low point를 확인하여 필요시 쉽게 접근이 가능한 곳에 drain valve를 설치한다. dryout시 주기적으로 drain valve를 이용하여 free water를 제거하며 이 목적으로 최소 1" drain valve를 고려한다.
Provisions for stagnant process areas
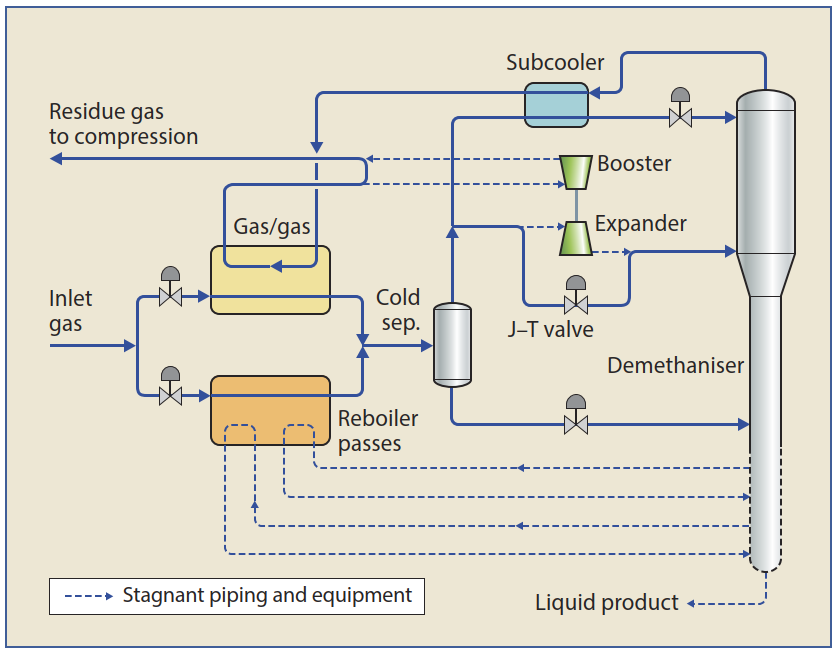
상기 도면은 dryout시 cold plant를 통한 main recirculation flow path와 stagnant area를 highlight하고 있다. dryout flow가 없는 즉 stagnant area는 위의 점선으로 표시되며, flow가 도입되지 않을 경우 wet 상태로 유지될 것이다. 그래서 이 stagnent area로 dryout gas 흐름이 도입되도록 설계에 고려해야 하며 일반적으로 4" 정도면 적절하고 규모가 커질수록 이 배관 size도 비례적으로 커져야 한다.
#dryout#cryogenic#hydrate#cooldown#pressure_cycling#질소퍼지#once_through#Joule_Thomson#closed_loop#surge#stagnant
'공정설계' 카테고리의 다른 글
Merox 공정 이해 (0) | 2025.01.03 |
---|---|
POE (Polyolefin) Elastomer (0) | 2025.01.03 |
증류 공정의 heat pump 활용 (0) | 2024.12.27 |
DMF process 이해 (0) | 2024.12.27 |
EO / EG 공정 이해 (2) | 2024.12.26 |